水泥稳定碎石的生产主要包括以下关键步骤:
1. 原材料准备与检验:
水泥:作为稳定剂,其质量至关重要。应选用符合规定要求的水泥,如普通硅酸盐水泥,强度等级一般为32.5或42.5,且初凝时间应大于3小时,终凝时间应大于6小时且小于10小时。
碎石:应选用洁净、干燥、无风化、无杂质的碎石,并按规定的粒径进行分级。例如,用做基层时,集料的最大粒径不应超过30mm。
水:拌合用水应符合相关标准,如饮用水可直接使用,非饮用水需进行水质检验。
对所有原材料进行严格的检验,确保其质量符合施工要求。
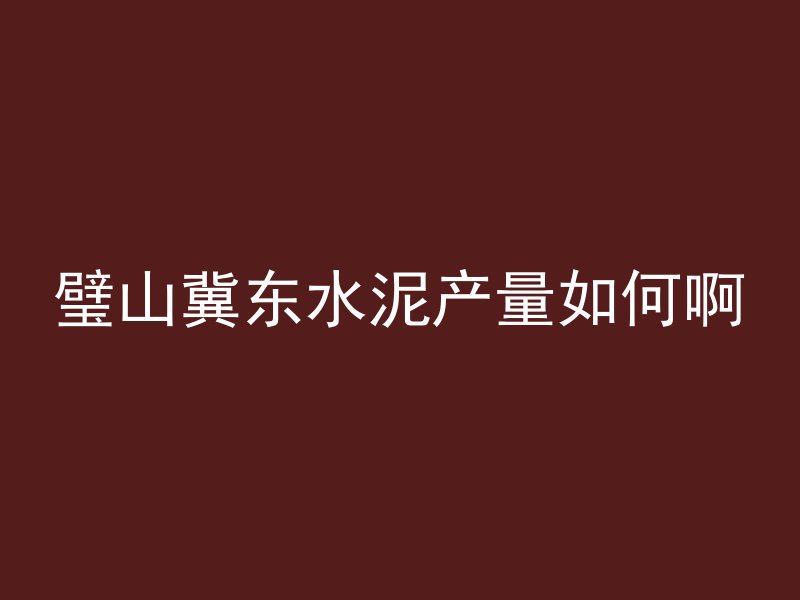
2. 混合料组成设计:
根据原材料的特点和性能,通过试验确定混合料的级配范围、水泥掺量、**含水量和最大干密度等参数。
进行目标配合比设计、生产配合比设计和施工参数确定,确保混合料的设计满足施工要求。
3. 拌合与运输:
在拌合站,按照试验室提供的配合比,将水泥、碎石和水等原材料进行准确计量和拌合,确保混合料的均匀性和质量。
拌合完成后,将混合料装入运输车辆,及时运送到施工现场。运输过程中应采取措施防止混合料离析和水分蒸发。
4. 摊铺与压实:
在施工现场,使用摊铺机将混合料均匀摊铺在路基上,确保摊铺厚度和平整度符合设计要求。
使用压路机对摊铺好的混合料进行压实,确保压实度达到规定要求。压实过程中应注意控制压实速度和遍数,避免过压或欠压。
5. 接缝处理与养生:
对于施工接缝,应采取有效措施进行处理,确保接缝处的平整度和密实性。
施工完成后,应对水泥稳定碎石基层进行养生,保持其湿润状态,以促进水泥的水化反应和强度的增长。
水泥稳定碎石的生产是一个涉及原材料准备、混合料设计、拌合与运输、摊铺与压实以及接缝处理与养生等多个环节的复杂过程。每个环节都需要严格控制质量和技术参数,以确保最终产品的性能和质量满足设计要求。