水泥罐挂车的生产是一个复杂而精细的过程,主要包括以下几个关键步骤:
1. 设计与规划:
采用三维立体设计方案,利用计算机将产品的实际形状表示成三维模型,这样可以更真实地反映出实际产品的构造和加工制造过程。
进行CAE受力分析,用计算机辅助分析出罐体的结构力学性能,并优化结构性能,使罐体受力更加合理,从而延长使用寿命。
2. 材料准备与切割:
选用高强度耐磨钢等优质材料,以确保罐体的耐用性和可靠性。
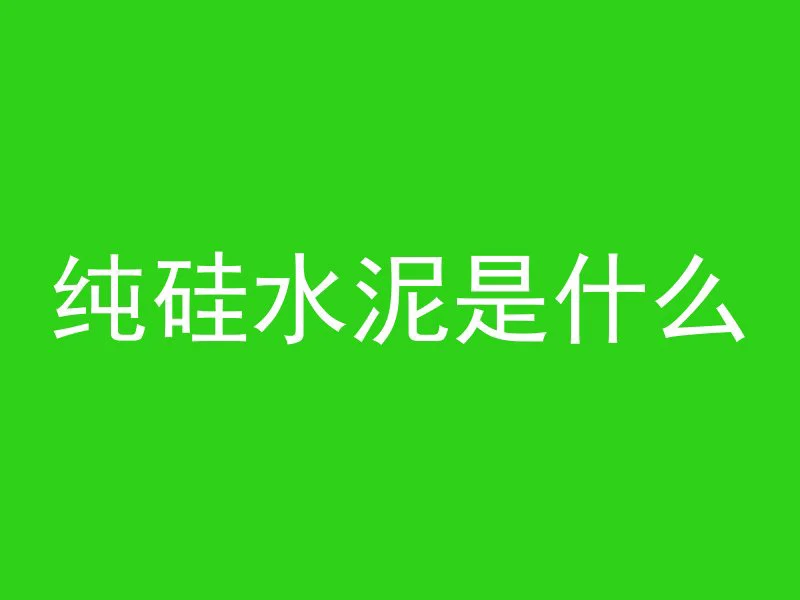
采用激光切割下料,提高精度到0.01mm,镜面切口一次成型,减少切割热熔面积,保持钢板元素的稳定性和刚性。
3. 罐体成型与组装:
使用自动化数控卷板机控制,使筒体一次成型,确保板材内部不会受损伤,成型质量稳定可靠。
采用框架式组队工艺,将左右滚筒对接,保证罐体组队过程不会变形。
4. 焊接与检测:
采用先进的机器进行焊接,确保焊缝的高质量、较长的使用寿命以及罐体的良好外观。
生产后,所有水泥罐半挂车都将通过压力测试和金属检查测试,以确保具有良好的密封性能。
5. 总装与调试:
罐体完成后,与底盘进行总装,底盘通常采用各种生产厂商的专用底盘,技术先进,性能可靠。
进行必要的调试和检测,确保水泥罐挂车的各项性能指标达到设计要求。
6. 质量检验与出厂:
对生产完成的水泥罐挂车进行全面的质量检验,包括外观、性能、安全性等方面。
通过质量检验后,水泥罐挂车即可出厂,交付给客户使用。
水泥罐挂车的生产过程涉及设计、材料准备、罐体成型、焊接、总装与调试以及质量检验等多个环节,每个环节都需要严格的质量控制和技术支持,以确保生产出的水泥罐挂车具有优良的性能和可靠的质量。这一系列复杂的工艺和流程共同构成了水泥罐挂车的生产过程。