在构建行吊轨道的基础时,选择合适的混凝土至关重要,它不仅关乎轨道的稳定性,还直接影响到行吊作业的安全与效率。
1. 强度要求
行吊轨道需承受重载机械频繁移动及作业时的巨大压力,混凝土必须具备足够的抗压强度。通常,C30至C50等级的高强度混凝土是首选,以确保长期承载下的结构稳定。
2. 耐久性考量
考虑到行吊轨道多暴露于户外环境,混凝土需具备良好的耐久性,抵抗风化、冻融循环及化学侵蚀。添加适量的引气剂或矿物掺合料,如粉煤灰、硅灰,能有效提升混凝土的耐久性。
3. 抗裂性能
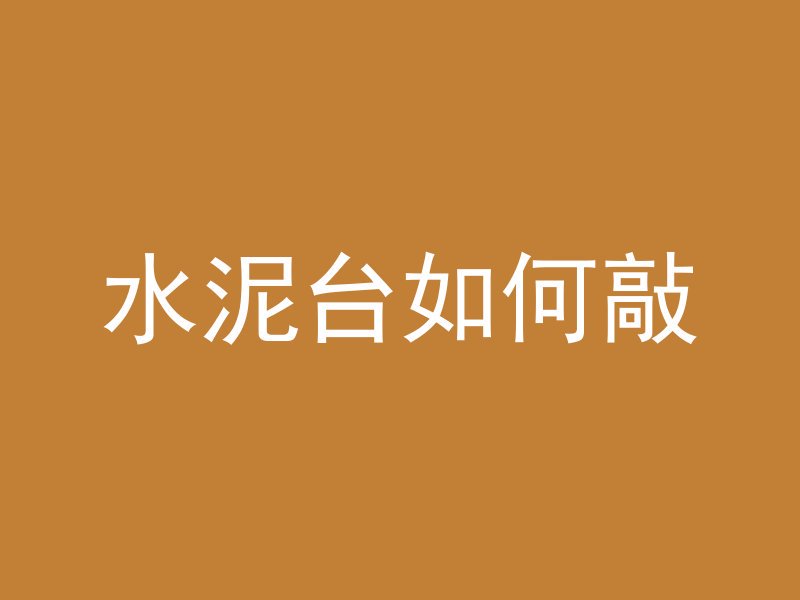
行吊作业产生的动态荷载易导致混凝土开裂,选用低热水泥、控制水灰比、加入纤维增强材料等措施,可显著提高混凝土的抗裂性,延长使用寿命。
4. 工作性能
良好的和易性是确保混凝土顺利浇筑、振捣密实的关键。通过调整混凝土配合比,使用高效减水剂,可使混凝土在保持高强度的具备良好的流动性和自密实性。
5. 固化时间
行吊轨道施工往往要求快速投入使用,选择早强型水泥或添加早强剂,可以缩短混凝土的硬化时间,加快工程进度。
6. 体积稳定性
混凝土在硬化过程中的体积变化需严格控制,以避免因收缩或膨胀导致的轨道变形。采用补偿收缩混凝土或添加膨胀剂,可有效维持轨道的几何精度。
7. 耐磨性增强
行吊车轮对轨道的磨损不容忽视,通过在混凝土表面添加耐磨骨料或采用耐磨地坪技术,能显著提升轨道表面的耐磨性能。
8. 环保要求
随着环保意识的增强,选择绿色混凝土材料,如再生骨料混凝土,减少碳排放,成为行业趋势。应关注混凝土生产过程中的能源消耗和环境污染问题。
9. 成本效益分析
在满足上述性能要求的还需综合考虑混凝土的成本效益。通过优化配合比、利用当地材料资源、提高施工效率等措施,实现性能与成本的**平衡。
行吊轨道所需的混凝土需综合考虑强度、耐久性、抗裂性、工作性能、固化时间、体积稳定性、耐磨性、环保性及成本效益等多个方面,以确保轨道的安全、高效运行。通过科学合理的选材与施工,为行吊作业提供坚实的基础支撑。