混凝土离析是混凝土拌合物组成材料之间粘聚力不足,导致粗集料下沉,与砂浆相互分离的现象。这一现象不仅影响混凝土的均匀性和稳定性,还可能对工程质量造成严重影响。下面将从多个方面详细阐述混凝土离析现象。
离析的定义与表现
混凝土离析主要表现为粗集料与砂浆的分离。当混凝土拌合物堆成一堆时,拌合物的流动性很好,但在放置一段时间后,表面会泌出稀浆,石子露出且表面不沾砂浆,砂石下沉紧贴底板,难以铲动,这被称为“扒底”。
离析的原因
离析的原因多种多样。浇筑和振捣不当是常见原因,如振捣过度或不足都可能导致离析。集料最大粒径过大、粗集料比例过高、胶凝材料和细集料的含量偏低也会引发离析。水泥质量的波动,如细度减小或含碱量变化,都可能影响混凝土的粘聚性,导致离析。
外加剂的影响
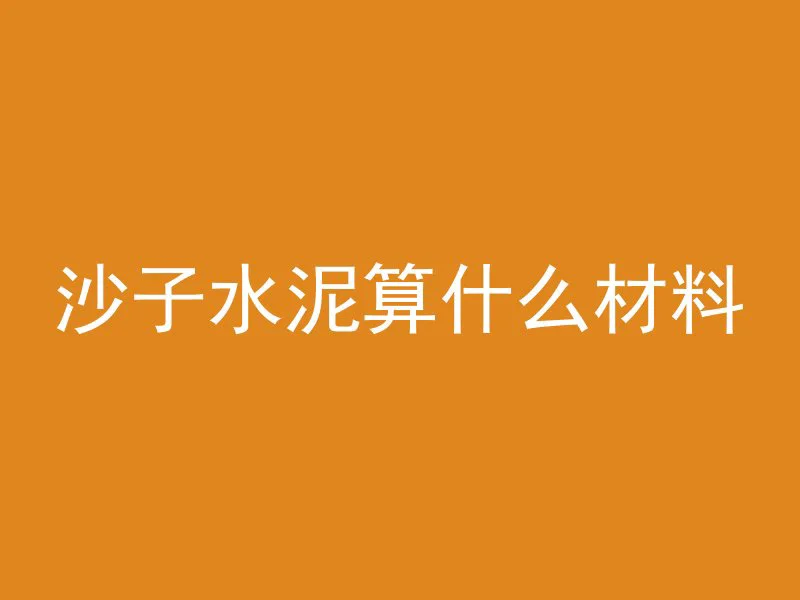
外加剂的使用对混凝土离析也有显著影响。减水剂掺量过大或过小都可能引起离析。减水剂掺量过大时,混凝土过于干燥,减水剂在搅拌机内未充分发挥作用,而在运输过程中继续作用,导致现场坍落度大于出机时,引发离析。而外加剂中缓凝组分、保塑组分掺量过大,也容易造成混凝土离析。
骨料与级配问题
骨料的质量和级配也是影响混凝土离析的重要因素。骨料粒径不均匀、级配不良都可能导致离析。粗骨料粒径过大或过小,都会使骨料在混凝土中的分布不均匀,从而引起离析。砂石料中的含泥量过高或含水量过大,也会影响混凝土的稳定性和流动性,导致离析。
水灰比与搅拌均匀性
水灰比过大也是混凝土离析的常见原因。水灰比过大会增加混凝土的流动性,使骨料易于沉积在底部,水泥浆体浮于表面。混凝土搅拌不均匀也会导致骨料与水泥浆体分离,造成离析。
离析的危害
混凝土离析对工程质量有诸多危害。离析的混凝土容易造成堵泵,影响施工效率。离析后的混凝土强度大幅度下降,严重影响混凝土结构承载能力,破坏结构的安全性能。离析还会导致混凝土表面出现砂纹、骨料外露、钢筋外露等现象,影响混凝土的表观效果。
预防措施
为了防止混凝土离析,可以采取多种预防措施。应严格控制原材料的质量,特别是水泥和骨料的质量。合理控制水灰比和外加剂的掺量,确保混凝土的流动性和粘聚性达到平衡。加强混凝土的搅拌过程管理,确保搅拌均匀充分。在混凝土运输和浇筑过程中,也应注意避免过度振捣和不当操作。
检测与调整
在混凝土生产过程中,应加强对混凝土拌合物的检测和调整。每天新开盘的第一车混凝土必须放料检测混凝土的和易性,查看拌合物是否存在离析。若发现离析现象,应及时调整配合比或采取其他补救措施。在搅拌过程中主要观察卸料时的搅拌电流,若发现电流异常,应提醒试验员取样检测。
混凝土离析是一个复杂且严重的问题,涉及多个方面的因素。只有深入了解离析的原因和危害,并采取有效的预防措施和检测调整方法,才能确保混凝土的质量稳定和施工顺利进行。