在路面打混凝土施工过程中,卸料环节至关重要,它直接影响到混凝土的质量与施工效率。下面将从多个方面详细阐述如何科学、高效地进行路面打混凝土的卸料操作。
1. 卸料前准备
卸料前,需确保施工现场已做好充分准备。检查卸料区域是否平整坚实,避免车辆陷入或倾斜。清理周边杂物,保持通道畅通无阻。确认混凝土搅拌车的罐体旋转方向正确,避免卸料时发生意外。
2. 选择合适卸料点
根据施工计划,选择**的卸料点。通常,卸料点应靠近浇筑区域,减少混凝土运输距离,避免混凝土在运输过程中分离或初凝。考虑卸料点的地形地貌,确保车辆能够稳定停放,便于卸料操作。
3. 控制卸料速度
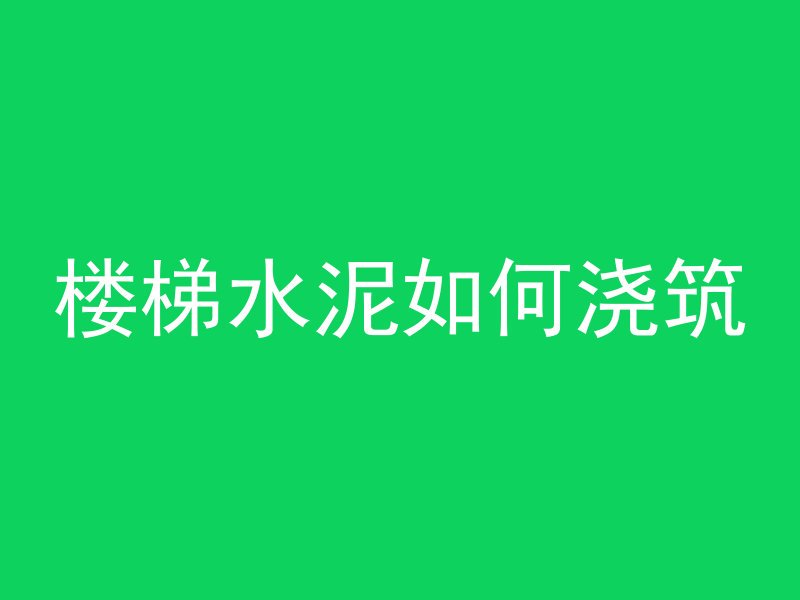
卸料速度是影响混凝土质量的关键因素之一。过快的卸料速度可能导致混凝土飞溅、分层或产生大量气泡。操作员应熟练掌握搅拌车的卸料控制,根据现场情况适时调整卸料速度,确保混凝土均匀流出。
4. 分层卸料与振捣
为保证混凝土层的密实度和均匀性,应采用分层卸料的方法。每层卸料后,及时用振捣棒或振捣板进行振捣,使混凝土充分密实,排除多余的气泡和水分。注意振捣的频率和力度,避免过振导致混凝土离析。
5. 观察混凝土状态
在卸料过程中,操作员应密切观察混凝土的状态,包括其流动性、颜色、稠度等。如发现异常,如混凝土过稀、过稠或含有大块杂质,应立即停止卸料,并通知相关人员进行处理。
6. 避免混凝土堆积
卸料时,应尽量避免混凝土在某一区域堆积过高,以免造成浇筑困难或混凝土内部应力集中。可通过移动卸料点或使用刮板等工具,使混凝土均匀分布在整个浇筑区域内。
7. 确保安全操作
安全是卸料过程中的首要考虑因素。操作员应穿戴好个人防护装备,如安全帽、防护眼镜、手套等。确保施工现场有专人指挥交通,避免车辆碰撞或人员受伤。
8. 清理与保养设备
卸料完成后,应及时清理搅拌车罐体及卸料区域,避免混凝土残留导致设备损坏或影响下次使用。定期对搅拌车进行保养和维护,确保其处于良好工作状态。
路面打混凝土的卸料环节需综合考虑多个因素,从准备到操作再到后续清理,每一步都需严格把控。通过科学合理的卸料方法,不仅可以提高施工效率,还能确保混凝土的质量和安全。