在混凝土浇筑过程中,振动是确保混凝土均匀密实、提高结构强度的关键步骤。有时我们可能会遇到混凝土不振动的情况,这不仅影响施工质量,还可能对结构安全构成威胁。接下来,我们将从多个方面深入探讨浇筑混凝土不振动的原因及应对措施。
1. 混凝土配合比问题
混凝土配合比的不合理是导致不振动的常见原因之一。若水灰比过大,混凝土过于稀薄,振动时难以形成有效的密实结构。相反,水灰比过小则混凝土过于干硬,振动难以使其均匀分布。应严格控制混凝土配合比,确保其在**范围内。
为优化配合比,可参考相关标准或进行试验,找到最适合当前工程条件的配合比。加强原材料管理,确保水泥、砂石等质量稳定,也是减少配合比问题的重要途径。
2. 振动设备故障
振动设备是混凝土浇筑中的关键工具,其性能直接影响振动效果。若振动设备出现故障,如振动频率不足、振幅过小或损坏等,都会导致混凝土不振动。应定期对振动设备进行检查和维护,确保其处于良好工作状态。
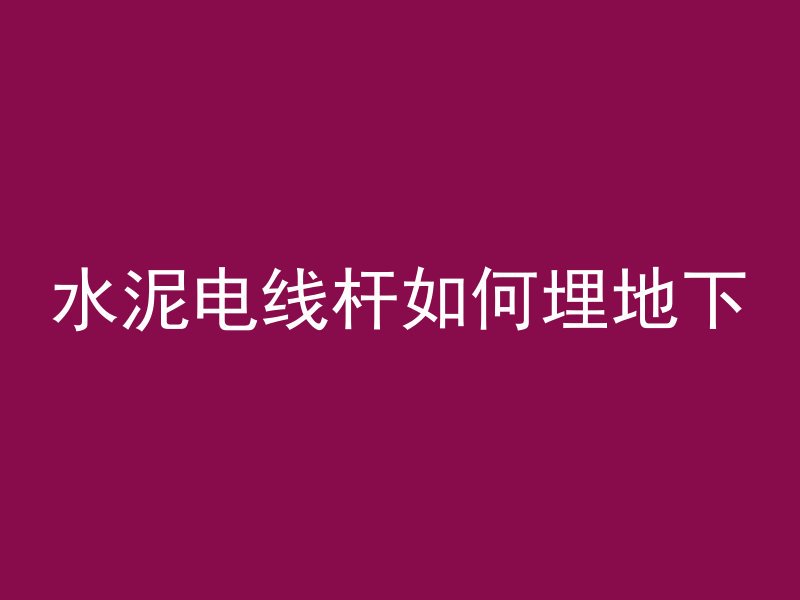
在浇筑前,操作人员应对振动设备进行试运转,确认其各项性能指标符合要求。浇筑过程中,若发现振动效果不佳,应立即停机检查并排除故障。
3. 振动操作不当
振动操作不当也是导致混凝土不振动的重要原因。如振动时间不足、振动位置不当或振动方式不合理等,都会影响混凝土的密实度和均匀性。操作人员应经过专业培训,掌握正确的振动操作方法。
在振动过程中,应遵循“快插慢拔、梅花形布置”的原则,确保每个振动点都能得到充分的振动。根据混凝土的坍落度和结构要求,合理调整振动时间和振动频率。
4. 模板问题
模板的刚度和稳定性对混凝土浇筑的振动效果也有很大影响。若模板变形或支撑不稳,会导致混凝土在振动过程中产生漏浆或跑模现象,从而影响振动效果。应加强对模板的检查和验收工作。
在浇筑前,应对模板进行全面检查,确保其平整度、垂直度和刚度符合要求。加强模板的支撑和固定措施,防止在振动过程中发生变形或位移。
5. 混凝土运输与浇筑时间
混凝土的运输和浇筑时间也会影响其振动效果。若混凝土在运输过程中时间过长或受到剧烈颠簸,会导致其分层离析现象加重,从而影响振动后的密实度和均匀性。应合理安排混凝土的运输和浇筑时间。
在运输过程中,应尽量选择平稳的道路和合适的运输工具,减少混凝土的颠簸和分层离析现象。根据工程实际情况和气候条件等因素,合理确定混凝土的浇筑时间,确保其在**状态下进行浇筑和振动。
6. 环境因素
环境因素如温度、湿度和风速等也会对混凝土的振动效果产生一定影响。在高温或干燥环境下,混凝土的水分蒸发较快,容易导致其过早凝固而影响振动效果。而在大风环境下进行浇筑和振动时,则容易使混凝土表面产生裂纹或麻面等现象。
为减少环境因素对混凝土振动效果的影响,应根据实际情况采取相应措施。如在高温或干燥环境下浇筑时,可采取喷雾降温或覆盖保湿等措施;在大风环境下浇筑时,则可采取挡风或调整振动方式等措施。
浇筑混凝土不振动的原因可能涉及多个方面。为确保施工质量和结构安全,我们应从配合比、振动设备、操作技术、模板问题、运输与浇筑时间以及环境因素等多个方面入手,采取有效措施加以防范和应对。