在建筑工程中,混凝土的质量至关重要,而气孔问题往往影响其性能与耐久性。如何确保混凝土没气孔,成为了业界关注的焦点。以下从多个方面详细探讨这一问题。
1. 选材控制
从原材料入手是关键。选用低含气量的水泥,减少因水泥自身带来的气孔。严格筛选骨料,避免使用含泥量高或孔隙率大的骨料,以减少混凝土中的孔隙来源。外加剂的选择也需谨慎,应选用与水泥适应性好的减水剂,以降低混凝土拌合物的气泡含量。
2. 配合比优化
合理的配合比设计对于减少气孔至关重要。通过调整水灰比、砂率等参数,可以找到使混凝土密实性**的配合比。研究表明,适当降低水灰比有助于减少气孔的形成,但需注意保持混凝土的工作性。砂率的调整也能有效影响混凝土的孔隙结构,需根据具体情况进行试验确定。
3. 搅拌工艺
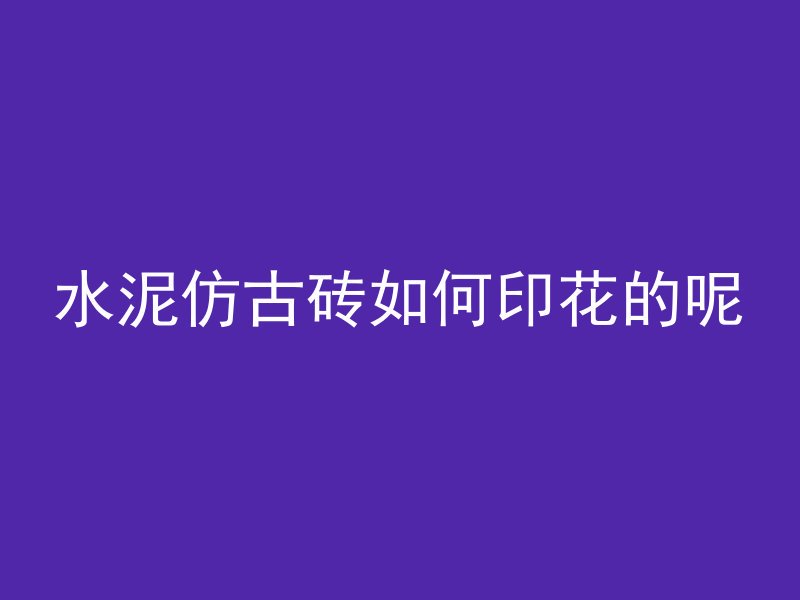
搅拌过程中,应确保混凝土拌合物充分均匀,避免局部气泡聚集。采用高效搅拌设备,延长搅拌时间,并合理控制搅拌速度,有助于气泡的分散与排出。搅拌顺序也需注意,先加入骨料和水,再逐步加入水泥和外加剂,可减少气泡的产生。
4. 振捣技术
振捣是混凝土施工中不可或缺的一环。通过有效的振捣,可以使混凝土拌合物更加密实,排出其中的气泡。振捣应选择在混凝土初凝前进行,且振捣棒应插入混凝土内部,确保振捣均匀。振捣时间需根据混凝土的性能和施工现场情况灵活调整。
5. 浇筑与养护
浇筑过程中,应控制浇筑速度,避免混凝土产生分层和气泡。浇筑后的养护也至关重要。适当的养护条件可以促进混凝土的水化反应,提高其密实性。养护期间,应保持混凝土表面湿润,避免快速干燥导致的气孔形成。
6. 添加剂使用
除了常规的减水剂外,还可以考虑使用消泡剂等特殊添加剂来减少混凝土中的气孔。这些添加剂能够破坏气泡的稳定性,使其更容易排出混凝土体系。但使用时需严格控制添加量,以免对混凝土的其他性能产生不良影响。
7. 施工环境
8. 质量检测
对混凝土进行质量检测是确保其没气孔的重要手段。通过检测混凝土的密实度、孔隙率等指标,可以及时发现并处理气孔问题。对施工现场进行实时监控,确保施工过程的规范性和混凝土质量的稳定性。
确保混凝土没气孔需要从选材、配合比、搅拌、振捣、浇筑、养护、添加剂使用、施工环境以及质量检测等多个方面入手。通过综合运用这些措施,可以有效减少混凝土中的气孔,提高其性能与耐久性。