在混凝土施工过程中,腋下漏振是一个常见且严重的问题,它不仅影响混凝土的强度和耐久性,还可能导致结构安全隐患。采取有效措施防止腋下漏振至关重要。以下从多个方面详细阐述如何防止混凝土腋下漏振。
明确振捣工人责任
对振捣工人进行明确的分工,责任到人,调动其生产积极性。将振捣质量与工资奖金挂钩,增强工人的责任心。施工前,应对工人进行技术培训,确保他们掌握正确的振捣方法和技巧。
选择合适的振捣器
根据工程特点,选择适宜的振捣器。对于大型构件,宜采用附着式振动器在侧模和底模上振动,辅以插入式振捣器。对于钢筋密集部位,应使用插入式振捣棒捣实。确保振捣器功率足够,振捣力满足施工要求。
掌握合适的振捣时间
振捣时间的长短直接影响混凝土的质量。振捣时间过长会导致过振,使水泥浆上浮、骨料下沉,影响混凝土的均匀性和强度。振捣时间过短则会导致漏振,使混凝土内部存在孔洞和气泡。应掌握合适的振捣时间,确保混凝土密实无气泡。
确定**振捣间距
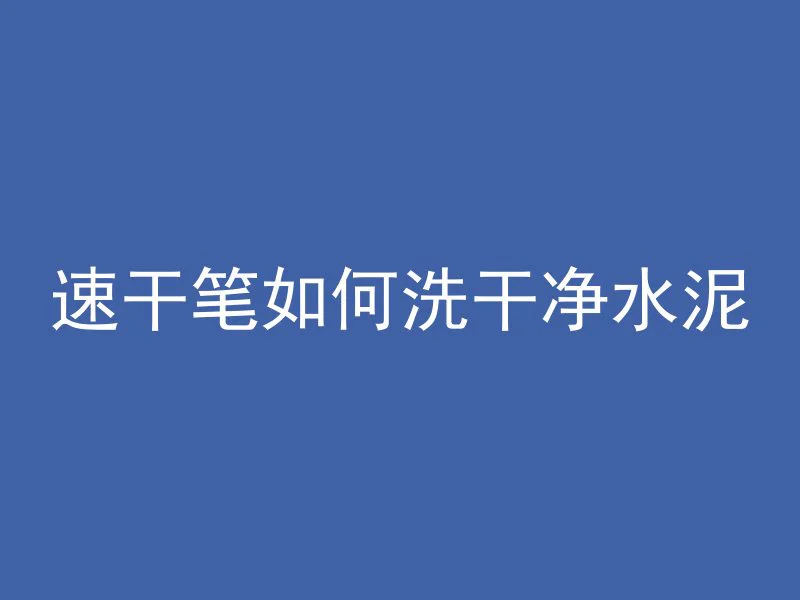
振捣间距的选择也是防止漏振的关键。振捣间距应略小于振捣半径,以确保振捣效果。对于插入式振捣器,振捣半径一般为45cm~75cm,振捣间距应在此范围内选择。平板振捣器的振捣厚度一般为20cm左右,移位间距应使振动器平板能覆盖已振实部分10cm左右。
分层浇筑振捣
混凝土应按一定厚度、顺序和方向分层浇筑振捣。分层厚度应适宜,插入式振捣器一般分层厚度为振捣棒头长度的0.8倍,平板振捣器分层厚度不宜大于20cm。上下层混凝土的振捣应重叠,以确保振捣效果。
采用正确的振捣方法
振捣时应采用正确的方法,插入速度要快,拔出速度要放慢,使混凝土内气体从底层逐渐赶到表层最后排出。振捣棒应慢慢插入混凝土中,避免撞击模板、钢筋等预埋件。振捣至混凝土顶面平整、泛浆、无气泡上浮、不再下沉且密实为止。
控制水灰比和外加剂含量
在满足施工要求坍落度的情况下,应尽量减小水灰比,同时控制外加剂中引气剂的含量不得大于规范规定的范围。水灰比越小,产生的气泡越少。外加剂中引气剂的质量对混凝土表面产生的气泡有本质影响,应选用引气气泡小、分布均匀稳定的引气型外加剂。
加强混凝土生产质量控制
在混凝土生产过程中,要加强质量控制,努力降低实际生产与试验之间的偏差。及时做好材料含水率检测,随时调整生产配合比,确保用水量和砂率与试配情况一致。加强混凝土的搅拌均匀性,避免产生离析和泌水现象。
使用消泡型脱模剂
市场上已有具有消泡化学成分的脱模剂,当混凝土产生的气泡与模板表面脱模剂中所含的消泡剂相遇后,消泡剂会立即破灭或由大变小,使混凝土表面达到平滑致密的效果。使用这种消泡型脱模剂可以有效减少混凝土表面的气泡。
实时监控浇筑过程
采用智能化的混凝土浇筑监控系统,通过传感器和数据分析技术实时监测混凝土的密实度和均匀性。及时发现并处理问题,确保混凝土在浇筑过程中得到充分振捣,避免出现漏振现象。
合理布置附着式振动器
对于使用附着式振动器的部位,应根据构造物形状及振动器性能等情况通过试验确定布置距离。确保振动器能够覆盖整个振捣区域,避免出现漏振现象。
注意浇筑连续性
在混凝土浇筑过程中,应保持连续性,避免出现长时间中断。若因特殊原因必须中断浇筑,其间断时间应小于前层混凝土的初凝时间,并充分注意前后浇筑混凝土的连结密实。若间断时间超出规定时间,一般按工作缝处理。
防止混凝土腋下漏振需要从多个方面入手,包括明确振捣工人责任、选择合适的振捣器、掌握合适的振捣时间和间距、分层浇筑振捣、采用正确的振捣方法、控制水灰比和外加剂含量、加强混凝土生产质量控制、使用消泡型脱模剂、实时监控浇筑过程、合理布置附着式振动器以及注意浇筑连续性等。只有全面考虑这些因素并采取有效措施,才能确保混凝土施工质量,避免出现腋下漏振等质量问题。