在建筑施工中,混凝土粘罐问题常困扰着工程人员。如何确保混凝土在搅拌、运输及浇筑过程中不粘罐体,成为提升施工效率与质量的关键。以下将从多个方面详细探讨解决之道。
1. 选用合适材料
混凝土的材料选择至关重要。使用高质量的水泥、骨料及外加剂,能有效减少混凝土对罐体的粘附。特别是外加剂,如减水剂、引气剂等,能显著改善混凝土的工作性,降低其粘黏性。研究表明,适量添加某些特殊外加剂,可使混凝土在罐体内壁形成一层薄薄的润滑膜,从而减少粘附。
2. 优化配合比设计
混凝土的配合比设计需考虑其流动性、粘聚性及保水性等性能指标。通过调整水灰比、砂率等参数,可使混凝土达到**的工作状态,既不过于干涩也不过于稀流,从而降低粘罐的风险。实践经验表明,合理的配合比设计能显著提高混凝土的泵送效率,减少粘罐现象。
3. 罐体预处理
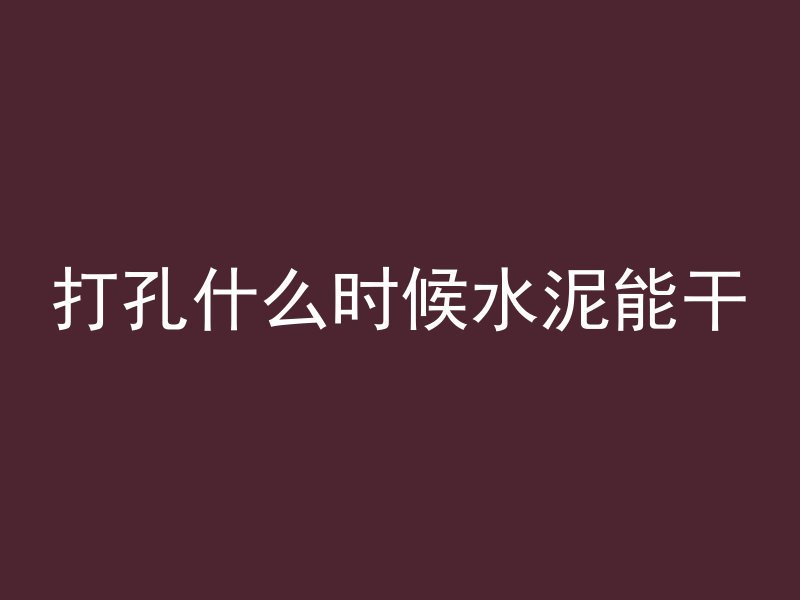
在混凝土搅拌或运输前,对罐体进行预处理也是关键一步。可通过喷涂防粘剂、涂抹润滑油或采用特殊涂层等方式,减少混凝土与罐体内壁的直接接触。这些预处理措施能形成一层隔离层,有效防止混凝土粘附。
4. 控制搅拌速度
搅拌速度是影响混凝土粘罐的重要因素。搅拌速度过快,可能导致混凝土过度搅拌而变得粘稠;搅拌速度过慢,则混凝土均匀性不足,也易粘罐。需根据混凝土的特性和施工要求,合理控制搅拌速度,确保混凝土处于**状态。
5. 定期清理罐体
定期清理罐体是保持其清洁、减少粘罐的有效方法。每次使用后,应及时清除罐体内残留的混凝土,避免其硬化后难以清理。定期检查罐体内壁是否有磨损或锈蚀现象,及时进行修复或更换。
6. 使用专业设备
采用专业的混凝土搅拌、运输及浇筑设备,也是减少粘罐的重要途径。这些设备通常设计有防粘功能,如特殊的搅拌叶片、光滑的罐体内壁等,能有效降低混凝土粘附的风险。
7. 调整浇筑方式
浇筑方式也影响混凝土的粘罐情况。采用合适的浇筑速度和角度,避免混凝土在罐体内停留时间过长或受到过大的冲击力,可减少粘罐现象。合理布置浇筑点,确保混凝土能顺利流入模具或施工部位。
8. 加强施工管理
加强施工管理也是预防混凝土粘罐的重要措施。应建立健全的施工管理制度,明确各环节的责任和操作规范,确保施工人员能严格按照要求进行操作。加强对施工人员的培训和教育,提高其专业技能和防范意识。
解决混凝土粘罐问题需从多个方面入手,包括选用合适材料、优化配合比设计、罐体预处理、控制搅拌速度、定期清理罐体、使用专业设备、调整浇筑方式及加强施工管理等。通过综合运用这些措施,可有效减少混凝土粘罐现象,提高施工效率与质量。