在建筑施工中,混凝土的质量与浇筑过程至关重要。想要避免混凝土闷罐,确保施工顺畅,就需从多个环节入手,精心策划与执行。以下将详细探讨如何有效防止混凝土闷罐,保证工程质量。
1. 选材与配比
优质的原材料是避免闷罐的基础。选用符合标准的水泥、砂石骨料及外加剂,确保混凝土性能稳定。合理的配合比设计也至关重要,通过试验确定**比例,既能满足强度要求,又能保持良好的工作性。
2. 搅拌工艺
搅拌过程中,应严格控制搅拌时间、速度和温度。过长的搅拌时间会导致混凝土过粘,易于闷罐;而搅拌不足则影响均匀性。采用高效节能的搅拌设备,确保混凝土各组分充分混合,达到**状态。
3. 运输管理
混凝土运输过程中,应尽量减少转运次数和距离,避免长时间等待。使用专用运输车辆,保持罐体清洁,防止残留物影响新拌混凝土质量。合理规划运输路线,确保混凝土在初凝前到达施工现场。
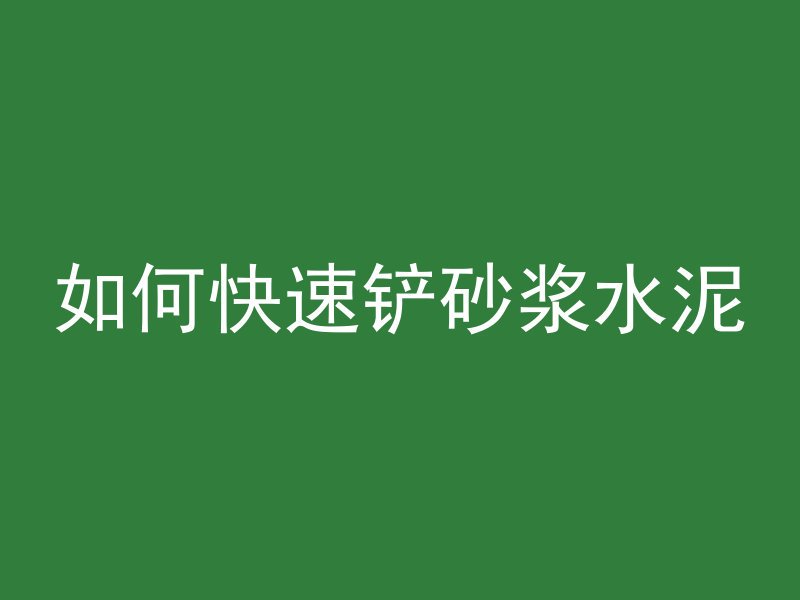
4. 泵送准备
泵送前,应仔细检查泵车及管道系统,确保无堵塞、无泄漏。根据泵送距离和高度,选择合适的泵送压力和流速。对泵送管道进行润滑处理,减少阻力,预防闷罐。
5. 现场浇筑
浇筑时,应分层进行,每层厚度不宜过大,以免混凝土内部产生过大压力。控制浇筑速度,避免过快导致混凝土来不及扩散而闷罐。使用振捣棒或振捣器辅助浇筑,提高混凝土密实度。
6. 温度控制
高温环境下,混凝土易因水分蒸发过快而变稠,增加闷罐风险。应采取遮阳、洒水等措施降低混凝土温度,保持其工作性。冬季施工时,则需采取保温措施,防止混凝土受冻。
7. 外加剂使用
合理使用外加剂,如减水剂、缓凝剂等,可有效改善混凝土工作性,减少闷罐概率。但需注意外加剂与混凝土的兼容性,以及过量使用可能带来的负面影响。
8. 人员培训
加强施工人员培训,提高其操作技能和应急处理能力。确保每位员工都能熟练掌握混凝土浇筑技巧,及时发现并处理闷罐等异常情况。
9. 设备维护
定期对搅拌站、泵车等设备进行维护保养,确保其处于良好工作状态。及时更换磨损部件,避免设备故障导致混凝土闷罐。
10. 监控与调整
施工过程中,应密切监控混凝土状态,根据实际情况及时调整配合比、泵送参数等。利用现代科技手段,如智能监控系统,实现施工过程的实时监控与数据分析,提高施工效率和质量。
避免混凝土闷罐需要从选材、搅拌、运输、泵送、浇筑等多个环节入手,综合运用技术和管理手段。通过不断优化施工工艺和加强质量控制,可以有效降低闷罐风险,确保混凝土施工质量和工程安全。