在建筑施工中,混凝土预制板的振捣是确保结构质量与性能的关键步骤。正确的振捣方法不仅能提高混凝土的密实度,还能增强其强度和耐久性。以下将从多个方面详细阐述混凝土预制板的振捣技巧。
1. 振捣前准备
在振捣前,需确保预制板模具清洁、无杂物,并涂抹适量的脱模剂。检查振捣设备是否完好,电源或动力源是否稳定。根据混凝土配合比,准备好所需材料,确保混凝土拌合物质量均匀。
2. 选择振捣设备
振捣设备的选择应依据预制板的尺寸、厚度及混凝土拌合物的特性而定。对于小型预制板,可采用手持式振捣棒;大型预制板则更适合使用振动台或振动平板。选用合适的设备能更有效地提高振捣效率和质量。
3. 振捣时间控制
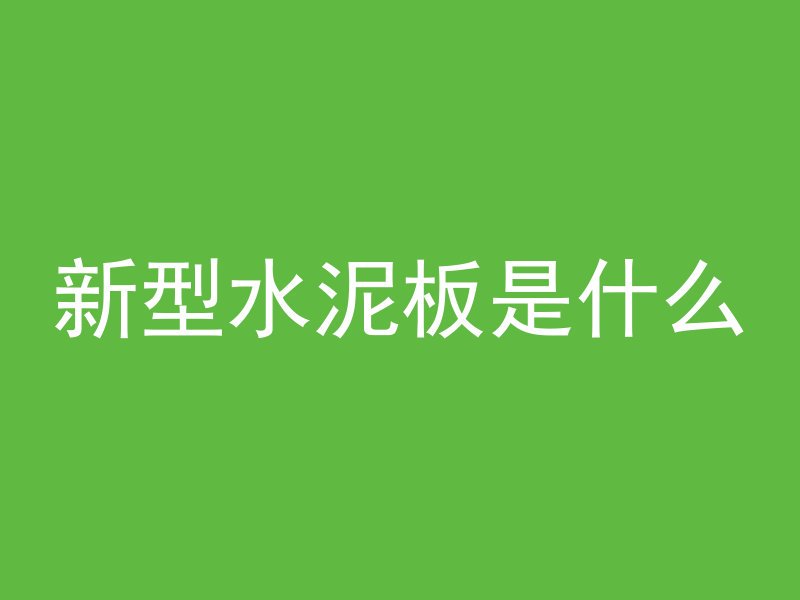
振捣时间的长短直接影响混凝土的密实度。振捣时间过短,混凝土内部孔隙多,强度低;振捣时间过长,则可能导致混凝土分层、泌水。需根据混凝土拌合物的稠度、温度及振捣设备的频率,合理控制振捣时间。
4. 振捣方式选择
振捣方式有连续振捣和间歇振捣两种。连续振捣适用于流动性较好的混凝土,能确保混凝土在整个振捣过程中保持均匀密实;间歇振捣则适用于较干的混凝土,通过多次短暂的振捣,逐步排出内部孔隙。
5. 振捣棒插入深度
使用振捣棒时,应控制其插入深度,确保振捣棒能深入混凝土内部,但又不至于触及模具底部或钢筋。一般插入深度为振捣棒有效长度的2/3至3/4,以确保混凝土各层都能得到充分振捣。
6. 振捣点布置
振捣点的布置应均匀合理,避免遗漏或重复振捣。对于大型预制板,可采用梅花形或棋盘形布置方式,确保每个区域都能得到有效振捣。
7. 避免过振与漏振
过振会导致混凝土分层、泌水,甚至产生裂缝;漏振则会使混凝土内部存在空洞,降低强度。在振捣过程中,需时刻关注混凝土的状态,及时调整振捣力度和时间。
8. 振捣后的处理
振捣完成后,应及时对混凝土表面进行抹平处理,消除表面气泡和裂纹。加强养护管理,确保混凝土在硬化过程中保持湿润,避免产生干缩裂缝。
9. 振捣效果检查
为验证振捣效果,可在预制板制作过程中进行取样检测。通过检测混凝土的密实度、强度等指标,评估振捣质量是否满足设计要求。
混凝土预制板的振捣是一个复杂而细致的过程。通过合理的准备、选择合适的设备、控制振捣时间、方式及深度,并注重振捣后的处理与效果检查,能有效提高预制板的质量与性能。在实际施工中,应结合具体情况灵活调整振捣方案,确保施工质量和安全。