在混凝土施工过程中,气泡的存在往往影响结构的密实度与美观性,有效排除气泡成为保证混凝土质量的关键步骤。以下将从多个角度详细探讨如何有效排出混凝土中的气泡。
1. 原材料控制
从源头上减少气泡的产生至关重要。选用低含气量的水泥、优质的骨料及外加剂,可以有效降低混凝土拌合物中的气泡含量。特别是外加剂的选择,如使用消泡剂,能显著减少搅拌过程中气泡的生成。
2. 拌合工艺优化
拌合过程中,应严格控制搅拌时间和速度。搅拌时间过长或过短都可能导致气泡分布不均或难以排出。通过调整搅拌机的转速和搅拌时间,使混凝土达到**的工作状态,有利于气泡的上升与排出。
3. 振捣技术
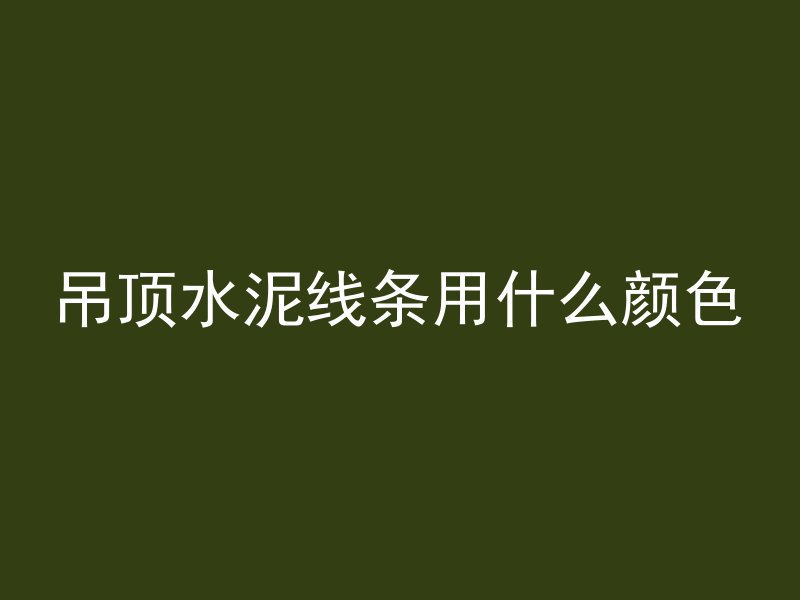
振捣是排除混凝土气泡的有效手段之一。采用合适的振捣设备,如插入式振捣棒或平板振捣器,根据混凝土的坍落度选择合适的振捣频率和力度,可以促使气泡向表面移动并最终破裂。振捣应均匀、连续,避免漏振或过振。
4. 浇筑方法
浇筑时,应采取分层浇筑、逐层振捣的方法,每层浇筑厚度不宜过大,以确保气泡有足够的时间上升至表面并排出。控制浇筑速度,避免混凝土堆积过高导致气泡难以逸出。
5. 模具设计
模具的设计也应考虑气泡的排出。模具表面应光滑无死角,便于气泡沿模具壁上升并排出。必要时,可在模具上开设排气孔,帮助内部气泡快速排出。
6. 真空脱气
对于高要求的混凝土制品,可采用真空脱气技术。通过真空泵抽取混凝土中的空气,形成负压环境,促使气泡迅速膨胀并破裂,从而达到排除气泡的目的。
7. 添加剂使用
除了消泡剂外,还可使用引气剂与减水剂配合,通过调整混凝土的气泡结构,使其更加细小且均匀分布,既提高了混凝土的耐久性,又减少了大气泡的产生。
8. 温度与湿度控制
混凝土拌合物的温度和湿度也会影响气泡的排出。过高的温度会加速气泡的上升速度,但可能导致混凝土过早凝固;湿度过大则可能阻碍气泡的排出。应合理控制施工环境的温湿度条件。
9. 后期处理
浇筑完成后,对于表面残留的气泡,可采用刮尺、抹刀等工具进行人工处理,进一步提高混凝土表面的平整度与美观性。
排出混凝土中的气泡需要综合考虑原材料、拌合工艺、振捣技术、浇筑方法、模具设计、真空脱气、添加剂使用以及温湿度控制等多个方面。通过科学合理的施工措施,可以有效减少气泡的产生与残留,提升混凝土的整体质量。