在建筑施工中,混凝土作为基础的建筑材料,其质量直接关系到整个工程的安全与耐久性。混凝土中常出现的气泡问题,却往往被忽视,成为潜在的质量隐患。那么,如何有效避免混凝土产生气泡呢?接下来,我们将从多个方面进行详细阐述。
1. 选材控制
从源头上把控,选择优质的混凝土原材料至关重要。水泥、骨料、外加剂等均应符合国家相关标准,特别是要关注水泥的细度、骨料的含泥量以及外加剂的适应性。这些材料的品质直接影响混凝土的拌合物性能,从而减少气泡的产生。
2. 配合比优化
合理的混凝土配合比设计是减少气泡的关键。通过调整水灰比、砂率、胶凝材料用量等参数,可以优化混凝土的流变性能,使其更易于密实,减少气泡的残留。考虑加入适量的引气剂,以在不影响混凝土强度的情况下,有效排除微小气泡。
3. 搅拌工艺
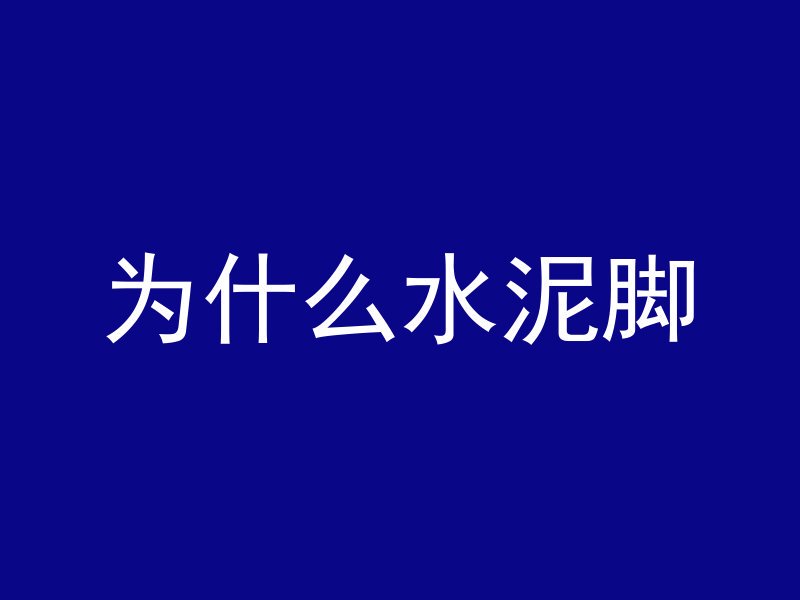
搅拌是混凝土制备过程中的重要环节。应确保搅拌时间足够,使各种材料充分混合均匀,避免局部过干或过湿导致的气泡产生。采用高效节能的搅拌设备,提高搅拌效率,也是减少气泡的有效手段。
4. 浇筑与振捣
浇筑时,应控制混凝土的自由落体高度,避免产生过大的冲击力导致气泡混入。加强振捣操作,使用合适的振捣设备,确保混凝土在模板内充分密实,排出气泡。振捣时间应适中,过长或过短都可能影响效果。
5. 模板处理
模板的清洁度与平整度对混凝土表面质量至关重要。浇筑前应彻底清理模板表面的杂物与灰尘,并涂抹适量的脱模剂,以减少气泡在模板上的附着。模板的接缝处应严密,防止漏浆导致的气泡产生。
6. 环境因素
施工环境对混凝土气泡的影响不容忽视。高温、大风等恶劣天气条件会加速混凝土的水分蒸发,导致气泡增多。应尽量避免在这些不利条件下施工,或在施工时采取相应的保湿、挡风措施。
7. 外加剂使用
外加剂的使用需谨慎。某些外加剂(如消泡剂)虽然能减少气泡,但过量使用可能影响混凝土的力学性能。在外加剂的选择上,应综合考虑其性能与混凝土的兼容性,并严格按照说明书使用。
8. 施工监控
加强施工过程中的质量监控,对混凝土拌合物的性能进行实时监测,及时发现并处理气泡问题。对施工人员进行专业培训,提高其操作水平与质量意识,也是减少气泡的有效途径。
9. 后期养护
混凝土浇筑完成后,应严格按照规范进行养护。适当的养护条件可以促进混凝土的水化反应,提高其密实度,从而减少气泡的残留。养护期间应避免混凝土受到剧烈的振动或冲击。
避免混凝土产生气泡需要从多个方面入手,包括选材控制、配合比优化、搅拌工艺、浇筑与振捣、模板处理、环境因素考虑、外加剂使用、施工监控以及后期养护等。只有综合考虑这些因素,并采取有效的措施,才能确保混凝土的质量与安全,为建筑工程的长期使用提供坚实保障。