在建筑施工中,混凝土作为最常用的建材之一,其质量直接关系到结构的稳固与安全。混凝土表面或内部出现气孔,不仅影响美观,还可能降低其耐久性和力学性能。那么,如何有效处理混凝土中的气孔问题呢?
1. 识别气孔成因
需准确判断气孔产生的原因。气孔可能由搅拌不均、振捣不足、模板漏气、添加剂使用不当等多种因素导致。通过细致检查施工记录和现场情况,可以为后续处理提供依据。
2. 优化配合比设计
调整混凝土的配合比,如减少水的用量、增加细集料比例,或选用合适的引气剂,可以有效减少气孔的产生。研究表明,合理的配合比设计能显著提高混凝土的密实度。
3. 加强搅拌与振捣
确保混凝土在搅拌过程中充分均匀,避免局部干料或湿料聚集。振捣时,应遵循“快插慢拔、梅花点布”的原则,确保振捣密实,特别是边角和难以振捣的部位。
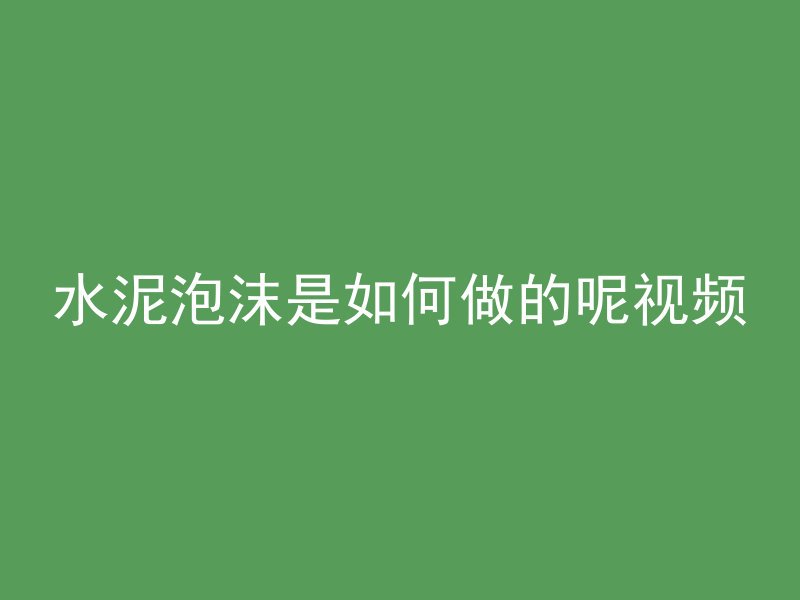
4. 改进模板工艺
模板应平整光滑,接缝紧密,防止漏浆。使用前需清理干净,并涂刷脱模剂。对于大型或复杂结构,可考虑采用钢模或铝模,以提高模板的刚度和密封性。
5. 控制浇筑速度
浇筑速度不宜过快,以免混凝土内部产生过多气泡。应分层浇筑,每层厚度控制在规定范围内,确保每层混凝土在初凝前被上一层覆盖。
6. 采用二次振捣技术
在混凝土初凝前进行二次振捣,可以进一步排除内部气泡,提高混凝土的密实度和强度。这一技术尤其适用于大体积混凝土或高性能混凝土。
7. 表面处理技术
对于已出现的表面气孔,可采用刮尺刮平、抹压或喷浆等方法进行修复。对于较大或较深的气孔,可先填充再打磨,确保表面平整光滑。
8. 加强养护管理
养护是减少混凝土气孔、提高其性能的关键环节。应严格按照规范进行湿养护,保持混凝土表面湿润,避免快速干燥导致的表面裂纹和气孔扩大。
9. 引入新技术新材料
随着科技的发展,越来越多的新技术和新材料被应用于混凝土领域。如使用自密实混凝土、添加特殊纤维或纳米材料等,都能有效减少气孔的产生。
10. 质量监控与验收
应加强对混凝土施工全过程的质量监控,包括原材料检验、配合比验证、施工过程检查及成品验收等。确保每一步都符合设计要求和质量标准。
处理混凝土中的气孔问题需要从多个方面入手,从源头预防到后期处理,每一步都至关重要。通过科学的管理和技术手段,可以有效减少气孔的产生,提高混凝土的质量和耐久性。