混凝土离析,这一术语描述了混凝土中粗骨料与水泥浆的分离现象,导致混凝土质地不均匀,进而影响其性能和强度。这一现象的发生涉及多个方面,下面将详细阐述。
1. 配合比设计不当
混凝土配合比设计是确保混凝土质量的关键。当水灰比过高或过低,水泥浆量不足,集料级配不合理时,都可能导致混凝土离析。例如,水灰比过大,混凝土会变得稀薄,易于在振动过程中发生离析。相反,如果胶凝材料太少,不足以将粗骨料充分包裹,也会导致粗骨料沉降,出现离析。
2. 搅拌不均匀
混凝土搅拌过程中,如果搅拌时间不足或搅拌速度不均匀,集料和水泥浆不能充分混合,也会导致离析。搅拌不充分会使混凝土中的材料分离,大颗粒骨料下沉到底部,水泥糊浆上浮到表面。
3. 运输过程中振动过大
混凝土在运输过程中,如果遭遇强烈的振动或冲击,也可能导致离析。振动会使混凝土中的集料和水泥浆分离,特别是在长距离运输或路况较差的情况下,这种影响更为显著。
4. 倾倒高度过高
混凝土在倾倒过程中,如果高度过高,会因重力的作用使集料和水泥浆分离。在浇筑时应尽量降低混凝土的垂直落差,避免离析现象的发生。
5. 施工操作不当
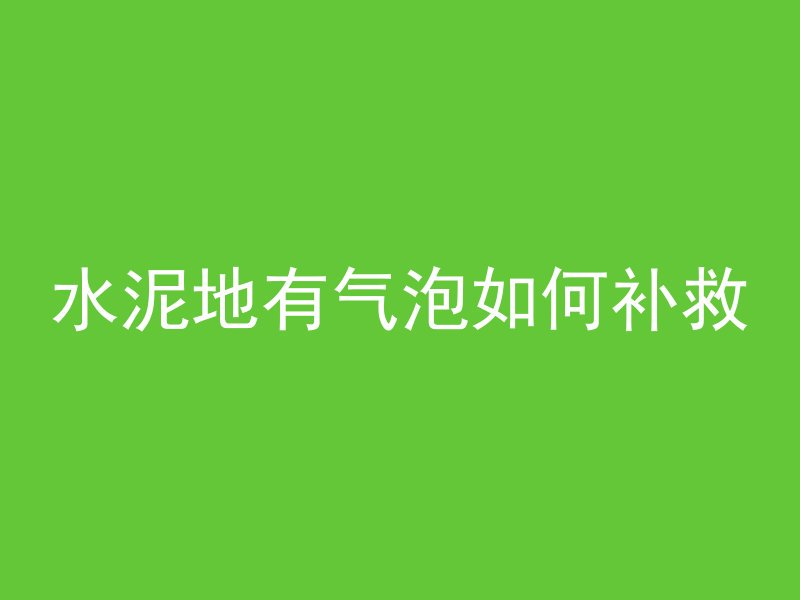
施工过程中的不当操作也是导致混凝土离析的重要原因。例如,浇筑速度过快、浇筑厚度过大、未能及时振捣等,都可能使混凝土中的集料和水泥浆分离。浇筑后立即进行表面抹平和收光作业,也可能导致粗骨料沉降,水泥浆上浮。
6. 环境因素
环境因素如温度和湿度对混凝土离析也有显著影响。高温会加快混凝土的凝固和固化速度,导致糊浆浓稠度降低,而低温则会延缓混凝土的凝固速度,增加离析的风险。干燥的环境也会使混凝土迅速失去水分,引发离析。
7. 骨料级配不合理
骨料的级配对混凝土的性能和离析现象起着重要作用。如果骨料配合不合理,如粗骨料过多或过少,细骨料过多或过少,都可能导致离析。粗骨料过多会增加混凝土的粘稠性,使混凝土在振动过程中更容易分离;细骨料过多则会减少混凝土的粘结性,同样导致离析。
8. 水泥质量不稳定
水泥作为混凝土中最主要的胶凝材料,其质量的稳定直接影响混凝土的质量。水泥细度的变化、矿物组分的变化以及存放时间的长短都可能影响混凝土的和易性,从而引发离析。例如,水泥细度下降可能导致减水剂过量,引发离析。
9. 外加剂使用不当
外加剂如缓凝剂、保塑剂、减水剂等在混凝土中起着重要作用,但如果使用不当,也可能导致离析。例如,减水剂掺量过大可能导致混凝土坍落度过大,引发离析。
10. 搅拌机质量或叶片磨损
现场搅拌混凝土时,如果搅拌机质量不好或叶片磨损严重,也可能导致混凝土离析。搅拌机质量不佳或叶片磨损会影响搅拌效果,使混凝土中的材料不能充分混合。
11. 混凝土垂直落差大
在施工过程中,如果混凝土从高处自由落下,垂直下落的距离过大,也可能导致离析。重力作用会使混凝土中的集料和水泥浆分离,特别是在没有采取有效缓冲措施的情况下。
12. 配筋过密
在钢筋混凝土结构中,如果配筋过密,也可能导致混凝土离析。密集的钢筋会阻碍混凝土的流动和振捣,使混凝土中的集料和水泥浆不能充分混合。
13. 随意加水
混凝土运送到施工现场后,如果工人随意向拌和物中加水,也会导致水灰比增大,水泥砂浆变稀,拌和物的粘聚性变差,从而产生离析。
14. 搅拌罐停转或转速过快
在混凝土运输过程中,如果搅拌罐停转或转速过快,也可能导致离析。搅拌罐停转会使混凝土中的材料相互脱离;而转速过快则会在离心力的作用下使较重的碎石子下沉。
15. 罐体设计不当
罐体内部搅拌叶片的安装设计角度以及做工等不合格也可能导致混凝土离析。合理的罐体设计和搅拌叶片布局是确保混凝土质量的关键。
混凝土离析是由多种因素综合作用的结果。为了避免和减少混凝土离析的发生,需要从配合比设计、搅拌、运输、倾倒、施工操作以及环境因素等多个方面加以控制和改进。加强对原材料的质量控制、优化施工工艺、提高施工人员的技术水平也是预防混凝土离析的重要措施。