混凝土表面出现气泡是一个常见问题,它严重影响混凝土的美观度和耐久性。为了有效修补混凝土气泡,需要从多个方面入手,采取科学合理的措施。
1. 气泡产生原因分析
混凝土气泡的产生往往与多种因素有关,包括原材料质量、配合比不合理、脱模剂选择不当、振捣方法不当等。例如,使用油性脱模剂相比水性脱模剂更容易产生气泡,而振捣不充分或分层过厚也可能导致气泡难以排除。
2. 选择合适的修补材料
针对混凝土表面气泡,首先需要选择合适的修补材料。对于直径小于2mm的气泡,通常可以不做处理;而对于直径大于2mm的气泡,则需要使用环氧胶泥等修补材料进行修补。修补材料的选择应根据气泡的大小和分布情况来确定。
3. 清洁处理气泡区域
在修补前,需要对气泡区域进行清洁处理。使用砂布或钢丝球将气泡周围的污垢、松散物质等清理干净,确保修补材料能够与混凝土表面良好粘结。还需要检查气泡内部是否有空气残留,必要时可用针将空出。
4. 涂刷填密封剂
对于表面气孔不是很明显的情况,可以使用填密封剂进行修补。在清洁干净混凝土表面后,将密封剂均匀地涂刷在气泡位置上,待干后再进行打磨处理,即可修复表面气泡。这种方法适用于气泡较小且分布均匀的情况。
5. 打磨表面并填充密封剂
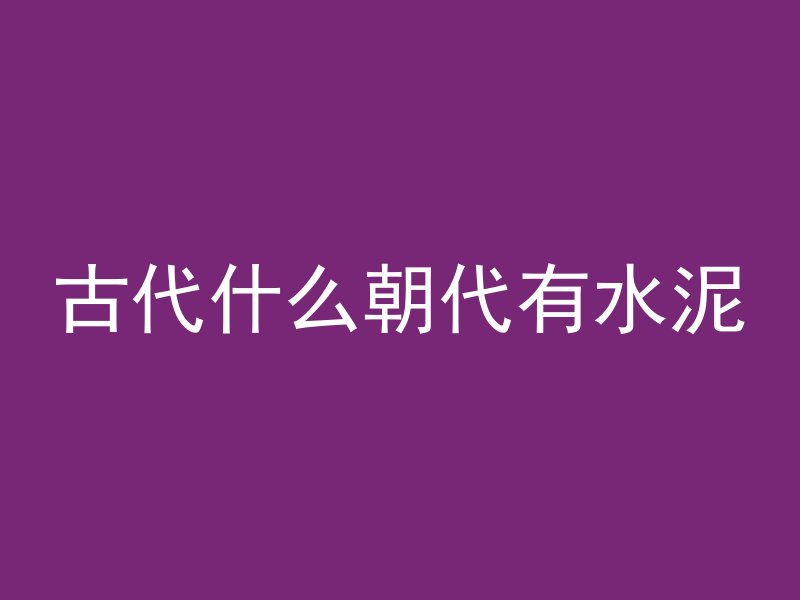
如果气泡较大或深度较深,可以先使用砂纸或打磨机对表面进行打磨处理,将气泡周围的不平整表面去除。然后填充密封剂进行修补,确保修补后的表面平整光滑。
6. 分层振捣与延长振捣时间
为了避免混凝土表面出现气泡,在搅拌和振捣过程中需要严格控制。分层进行振捣,每层厚度不宜过大,同时适当延长振捣时间,确保混凝土内部的结构更加密实。振捣时应采用“快插慢抽、上下抽拔”的方式,防止漏振和过振。
7. 添加消泡剂
在混凝土搅拌过程中,可以添加适量的硅醚共聚类的消泡剂,以有效降低混凝土产生的气泡数量。消泡剂的添加不会影响到混凝土的强度,但需要根据实际情况合理控制添加量。
8. 控制原材料质量
混凝土原材料的质量直接影响到混凝土的性能和质量。在原材料进场时需要严格把好关,对水泥、沙子、石头等材料进行严格检查和验收。特别是水泥,需要查看合格证、产品质量证书等材料,并进行抽样检查。
9. 严格控制配合比
混凝土的配合比对其性能和质量有着重要影响。在搅拌过程中,需要严格控制好材料配比,根据正确的配比进行调制。配料之前应先测量砂石的含水率,并根据实际情况进行适当调整。
10. 优选水性脱模剂
脱模剂的选择对气泡的产生有着重要影响。相比油性脱模剂,水性脱模剂产生气泡的概率更低。在条件允许的情况下,应优先选择水性脱模剂进行使用。
11. 模板处理与加固
模板的清洁度和加固情况也会影响到混凝土表面的气泡产生。每次使用模板前需要仔细清除表面残渣,保证模板的光洁度。还需要对模板进行加固处理,防止浇筑过程中出现漏浆和变形情况。
12. 养护与测温控制
混凝土浇筑后的养护工作同样重要。需要按照要求进行测温、控制湿度等养护措施,防止混凝土表面干裂和气泡产生。养护期间应注意保持混凝土表面的湿润和温度适宜。
13. 钢筋与混凝土接触处理
在浇筑混凝土时,应避免钢筋与混凝土表面直接接触。钢筋与混凝土表面接触容易产生气泡和麻面现象。在浇筑前应对钢筋进行妥善处理,确保其不与混凝土表面直接接触。
14. 修补后的表面处理
修补完成后,需要对修补表面进行处理。使用批处理工具将修补材料推平,使表面平整光滑。然后用塑料袋或透明覆盖物将修补表面遮盖起来,防止直接阳光照射和水分蒸发过快导致表面干裂。
15. 定期检查与维护
修补完成后,还需要定期对混凝土表面进行检查和维护。及时发现并处理新产生的气泡和麻面现象,确保混凝土表面的平整度和美观度。还需要对混凝土进行定期养护和维护工作,延长其使用寿命。
修补混凝土表面气泡需要从多个方面入手,采取科学合理的措施。通过选择合适的修补材料、清洁处理气泡区域、涂刷填密封剂、打磨表面并填充密封剂、分层振捣与延长振捣时间、添加消泡剂、控制原材料质量、严格控制配合比、优选水性脱模剂、模板处理与加固、养护与测温控制、钢筋与混凝土接触处理、修补后的表面处理和定期检查与维护等方法,可以有效解决混凝土表面气泡问题,提高混凝土的美观度和耐久性。