在混凝土施工中,气泡管理对于预防裂缝至关重要。通过科学控制气泡,不仅能提升混凝土的美观度,还能有效增强其结构性能,减少裂缝的产生,延长使用寿命。
1. 选用优质材料
从源头上把控,选用低碱、低气泡的水泥和外加剂。优质材料能显著减少混凝土拌合物中的气泡含量,为防裂打下坚实基础。合理搭配骨料,确保粒径分布均匀,减少因骨料间空隙过大而产生的气泡。
2. 优化配合比设计
通过试验确定**配合比,平衡水灰比、含气量等关键参数。适当降低水灰比可减少自由水,进而减少气泡的形成与聚集。根据工程需求调整含气量,既保证混凝土的耐久性,又避免气泡过多导致的裂缝风险。
3. 加强搅拌工艺
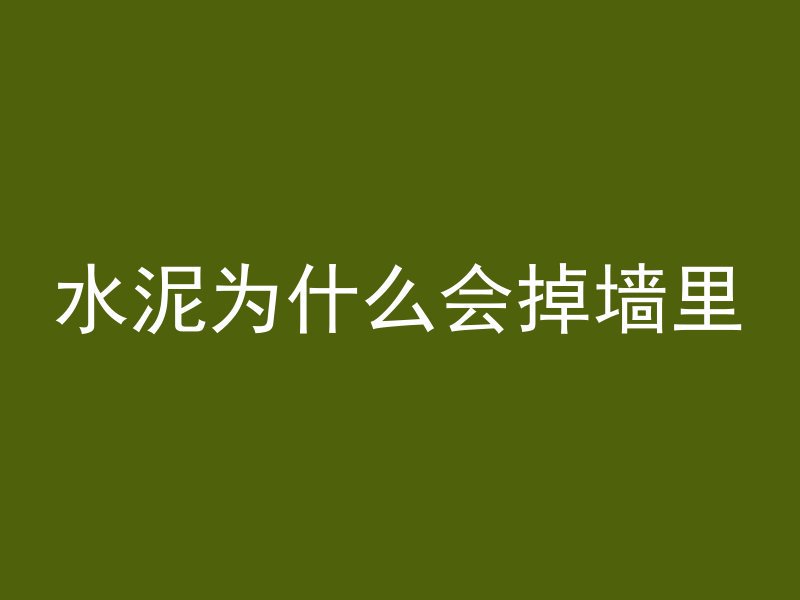
搅拌过程中,应确保搅拌均匀,避免局部过稠或过稀,减少气泡的生成。采用高效搅拌设备,延长搅拌时间,使外加剂充分分散,气泡得以有效排除。合理的投料顺序也能有效控制气泡的产生。
4. 振捣技术改进
振捣是消除气泡的关键步骤。采用高频低幅的振捣方式,确保混凝土内部气泡充分上浮并排出。振捣应均匀、密实,避免漏振或过振,以免破坏混凝土结构或引入新的气泡。
5. 控制浇筑速度
浇筑时,应控制浇筑速度,避免过快导致混凝土内部气泡无法及时排出。分层浇筑,每层厚度适中,确保气泡有足够的空间和时间上浮至表面。
6. 表面处理与养护
浇筑完成后,及时对混凝土表面进行抹压、刮平,进一步排除表面气泡。随后,采取适当的养护措施,如覆盖保湿、定期洒水等,保持混凝土表面湿润,减少因干燥收缩引起的裂缝。
7. 使用消泡剂
在特定情况下,可适量添加消泡剂,以降低混凝土拌合物中的气泡含量。但需注意消泡剂的类型与用量,以免对混凝土性能产生负面影响。
8. 监测与调整
施工过程中,应定期对混凝土的气泡含量、含气量等指标进行监测,并根据监测结果及时调整施工工艺和材料配合比,确保气泡控制效果。
通过选用优质材料、优化配合比设计、加强搅拌与振捣工艺、控制浇筑速度、注重表面处理与养护、合理使用消泡剂以及持续监测与调整,可以有效防止混凝土因气泡问题而产生的裂缝,提升工程质量与耐久性。