在混凝土施工过程中,气泡过多是一个常见且需重视的问题,它直接影响混凝土的密实度与强度。为有效解决这一问题,需从多个维度入手,细致调整,确保混凝土质量。
1. 调整配合比
应从混凝土的配合比着手。过多的气泡往往与水泥用量、水灰比及外加剂种类有关。通过适当减少水泥用量或调整水灰比,可降低混凝土拌合物中的自由水量,从而减少气泡产生。选用低气泡生成的外加剂也是关键,如引气剂需严格控制其掺量。
2. 优化搅拌工艺
搅拌过程中,搅拌速度和时间对气泡含量有显著影响。搅拌速度过快或时间过长,均可能导致气泡大量混入。应根据具体材料特性,合理设定搅拌参数,采用先慢后快、分段搅拌的方式,既保证材料均匀混合,又有效控制气泡生成。
3. 改进浇筑方法
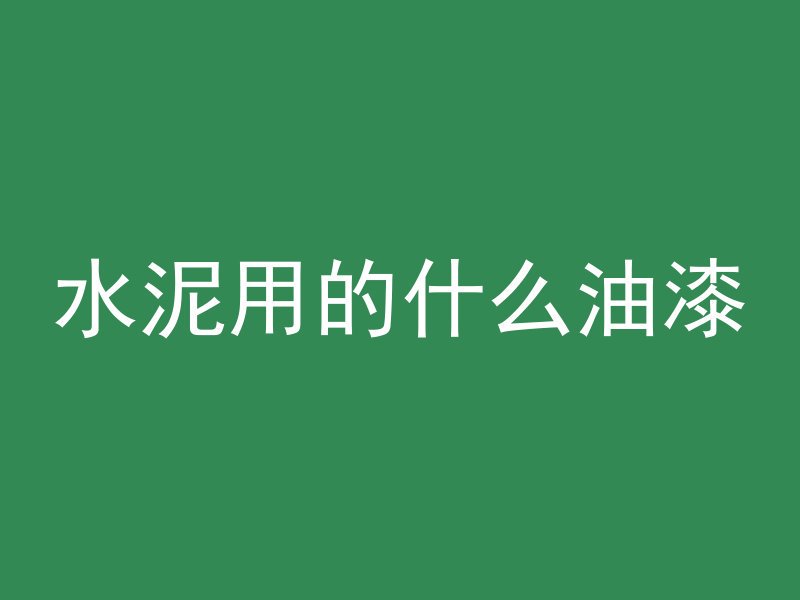
浇筑时,应避免混凝土自由落体高度过大,以减少因撞击产生的气泡。采用溜槽、导管等辅助工具,使混凝土平缓流入模内,可有效降低气泡含量。分层浇筑、振捣密实也是减少气泡的有效手段,每层浇筑后应及时振捣,确保混凝土内部气泡排出。
4. 加强振捣作业
振捣是消除混凝土内部气泡的关键步骤。应选择合适的振捣设备,如插入式振捣棒或平板振捣器,根据混凝土稠度调整振捣频率和持续时间。振捣应均匀、全面,避免漏振或过振,确保混凝土内部气泡充分排出,提高密实度。
5. 控制原材料质量
原材料的质量直接影响混凝土的气泡含量。应严格筛选砂石骨料,去除含泥量高、粒径不均匀的颗粒,减少因材料本身携带的气泡。水泥应选用品质稳定、气泡生成少的产品,从源头上控制气泡产生。
6. 调整养护条件
养护过程中,温度和湿度的控制对混凝土气泡的消除也有一定影响。适当的养护温度可促进水泥水化,减少气泡残留;而保持适宜的湿度则有助于混凝土内部水分均匀分布,避免气泡因水分蒸发而集中析出。
7. 引入消泡剂
在特定情况下,可考虑向混凝土中加入消泡剂,以化学方式降低气泡含量。消泡剂能破坏气泡表面张力,使其迅速破灭。但需注意,消泡剂的种类和掺量需经过试验确定,以免对混凝土性能产生负面影响。
8. 加强现场管理
加强施工现场的管理也是减少气泡的重要措施。应定期对施工人员进行培训,提高其操作技能和质量意识;建立严格的质量检查制度,对每批混凝土进行气泡含量检测,确保施工质量符合规范要求。
调整混凝土气泡过多需从配合比、搅拌工艺、浇筑方法、振捣作业、原材料质量、养护条件、消泡剂使用及现场管理等多个方面综合考虑,通过科学、细致的操作,有效降低气泡含量,提升混凝土的整体质量。