在混凝土施工中,气泡问题时常困扰着工程师与施工人员。气泡不仅影响混凝土的外观质量,还可能对其力学性能造成不利影响。那么,当混凝土内出现气泡时,我们应如何有效补救呢?
1. 识别气泡成因
需准确识别气泡产生的原因。混凝土内气泡多由于搅拌不均、材料含气量高、振捣不足或模板表面不光滑等因素导致。了解成因后,才能对症下药,采取有效补救措施。
2. 加强材料控制
选用低含气量的水泥、砂石等原材料,严格控制其质量。对于高含气量的材料,可通过预处理如筛分、洗涤等方式降低其含气量。合理调整配合比,确保混凝土拌合物的和易性。
3. 优化搅拌工艺
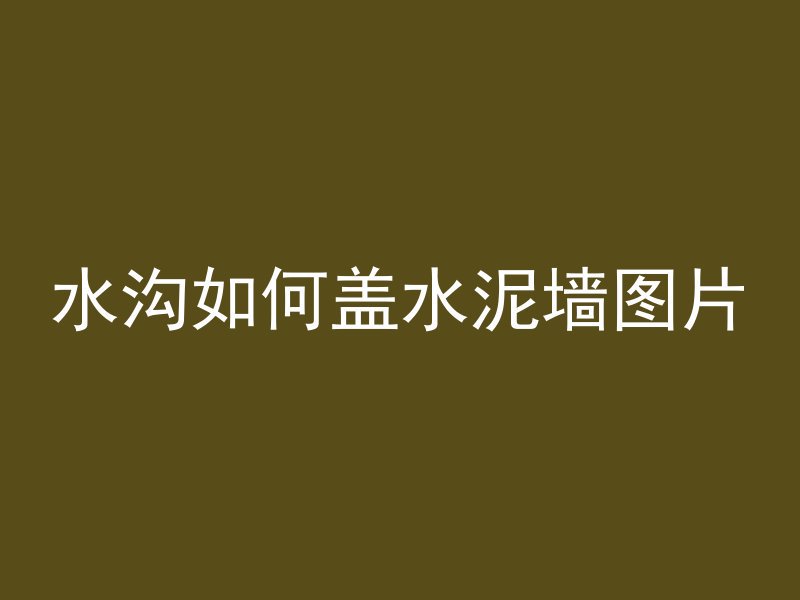
搅拌是混凝土制备的关键环节。应确保搅拌时间充足,使各组分充分混合均匀。采用高效的搅拌设备,如强制式搅拌机,可有效提高搅拌效率,减少气泡的产生。
4. 加强振捣操作
振捣是消除混凝土内气泡的有效手段。应选择合适的振捣设备,如插入式振捣棒或平板振捣器,并遵循正确的振捣方法。振捣时应均匀、连续,避免漏振或过振,以确保气泡被充分排出。
5. 改进模板工艺
模板的表面质量和安装精度直接影响混凝土的外观质量。应选用表面平整、光滑的模板,并在使用前进行清洁和涂油处理。确保模板安装牢固、密封性好,避免漏浆和气泡的产生。
6. 采用消泡剂
当混凝土内气泡问题严重时,可考虑添加消泡剂。消泡剂能够破坏气泡的稳定性,使其迅速消散。但应注意控制消泡剂的用量,避免对混凝土性能产生不良影响。
7. 二次振捣与抹面
在混凝土浇筑后,可进行二次振捣和抹面操作。二次振捣能够进一步排除混凝土内的气泡,提高混凝土的密实度。抹面则能够平整混凝土表面,减少气泡的残留。
8. 养护与检测
养护是混凝土强度发展的关键环节。应严格按照规范要求进行养护,确保混凝土充分水化。定期对混凝土进行检测,及时发现并处理气泡问题。
9. 预防措施
除了补救措施外,预防气泡的产生同样重要。应加强对原材料、搅拌、浇筑、振捣等各个环节的质量控制,从源头上减少气泡的产生。
混凝土内气泡的补救需要从多个方面入手,包括识别成因、加强材料控制、优化搅拌工艺、加强振捣操作、改进模板工艺、采用消泡剂、二次振捣与抹面、养护与检测以及预防措施等。只有综合运用这些措施,才能有效解决混凝土内气泡问题,提高混凝土的施工质量和力学性能。