在建筑施工中,混凝土面的压光是一项至关重要的工序,它直接影响着混凝土表面的美观度与耐久性。接下来,我们将深入探讨混凝土面压光的多个关键环节,以确保施工质量的提升建筑的整体效果。
1. 压光时机选择
混凝土浇筑完成后,需等待其初凝阶段再进行压光。过早压光易导致混凝土表面出现裂纹,而过晚则难以达到理想的压光效果。准确判断混凝土的初凝时间,是压光成功的第一步。
2. 表面处理准备
在压光前,应清除混凝土表面的浮浆、杂物及积水,确保表面干净、平整。这一步骤对于后续压光工作的顺利进行至关重要,也是保证压光质量的基础。
3. 压光工具选用
根据混凝土面的大小、形状及压光要求,选择合适的压光工具。常用的压光工具有木抹子、铁抹子、压光机等。不同工具的使用,会产生不同的压光效果,需根据实际需求灵活选用。
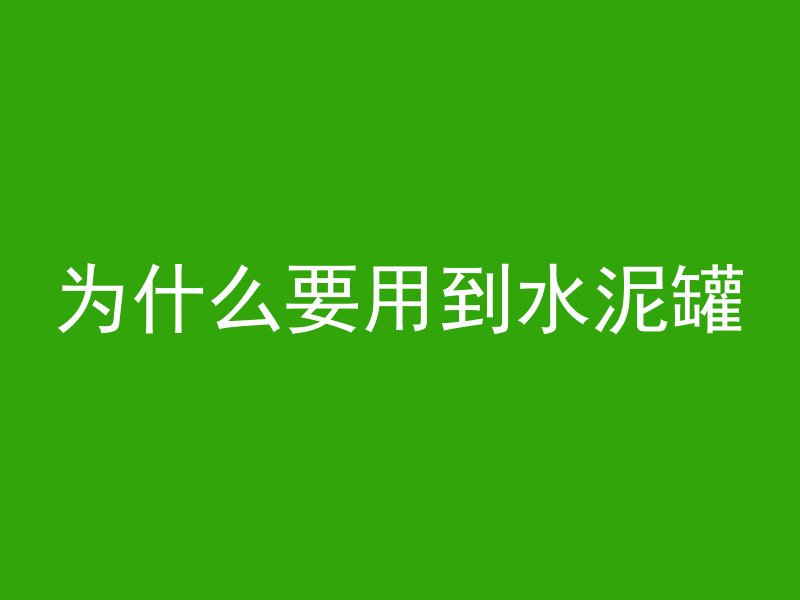
4. 初步压光操作
初步压光时,应使用较为粗糙的工具,如木抹子,以较大的力度均匀抹压混凝土表面。此阶段的目标是去除表面的不平整,使混凝土初步形成致密、平整的表层。
5. 精细压光处理
初步压光后,需换用更为细腻的工具,如铁抹子或压光机,进行精细压光。应减小抹压力度,以避免破坏已形成的平整表层。精细压光旨在进一步提升混凝土表面的光泽度与平整度。
6. 边缘与角落处理
对于混凝土面的边缘与角落,由于工具难以触及,需特别关注。可使用小型手动工具或特殊形状的压光工具进行细致处理,确保整个混凝土面压光效果均匀一致。
7. 压光次数控制
压光次数并非越多越好,需根据混凝土的性能、环境条件及压光要求综合考虑。过多的压光可能导致混凝土表面硬化过度,反而降低其耐久性。合理控制压光次数是确保压光质量的关键。
8. 水分管理
在压光过程中,应密切关注混凝土表面的水分情况。过干或过湿都会影响压光效果。必要时,可通过洒水或覆盖湿布等方式调节混凝土表面的水分含量。
9. 压光后养护
压光完成后,应及时对混凝土面进行养护。养护措施包括覆盖保湿材料、定期洒水等,以确保混凝土在硬化过程中保持适宜的水分条件,从而提高其强度与耐久性。
10. 质量控制与检查
压光过程中及完成后,应进行严格的质量控制与检查。通过目测、尺量等方式检查混凝土表面的平整度、光泽度及是否有裂纹等缺陷。发现问题应及时整改,确保压光质量符合设计要求。
混凝土面的压光是一项技术性较强的工序,需综合考虑多个因素并严格控制各个环节。通过科学合理的操作与管理,可以确保混凝土面达到理想的压光效果,为建筑的整体质量与美观度奠定坚实基础。