混凝土梁板施工中,气泡问题常常成为困扰工程师和施工人员的一大难题。气泡不仅影响混凝土的美观性,还可能对其力学性能和使用寿命产生不利影响。本文将从多个方面详细探讨混凝土梁板气泡多的原因。
1. 原材料因素
气泡的产生与水泥品种有密切关系。水泥在生产过程中使用助磨剂,这些助磨剂往往含有较多的表面活性剂,容易产生气泡。水泥的碱含量过高、细度过细也会增加气泡的数量。例如,某些复合硅酸盐水泥因混合材掺量过高,在配制混凝土时易产生气泡。
2. 骨料级配不合理
骨料级配不合理是导致气泡产生的另一个重要原因。粗骨料过多、大小不当,碎石中针片状颗粒含量过多,以及实际使用砂率偏低,都会导致细骨料不足以填充粗骨料之间的空隙,形成自由空隙,为气泡的产生提供了条件。
3. 外加剂的影响
外加剂如减水剂在混凝土中具有一定的引气效果。不同的类型和掺量都会影响气泡的数量和大小。例如,聚羧酸减水剂在混凝土中引入的气泡含量和质量不稳定,可能产生大的有害气泡,影响混凝土性能。
4. 水灰比不合理
水灰比偏大时,水泥浆浆体无法充分填充骨料空隙,导致气泡形成的概率增大。在水泥用量较少的混凝土中,由于水化反应耗费用水较少,使得薄膜结合水、自由水相对较多,从而增加了气泡形成的机率。
5. 搅拌时间不当
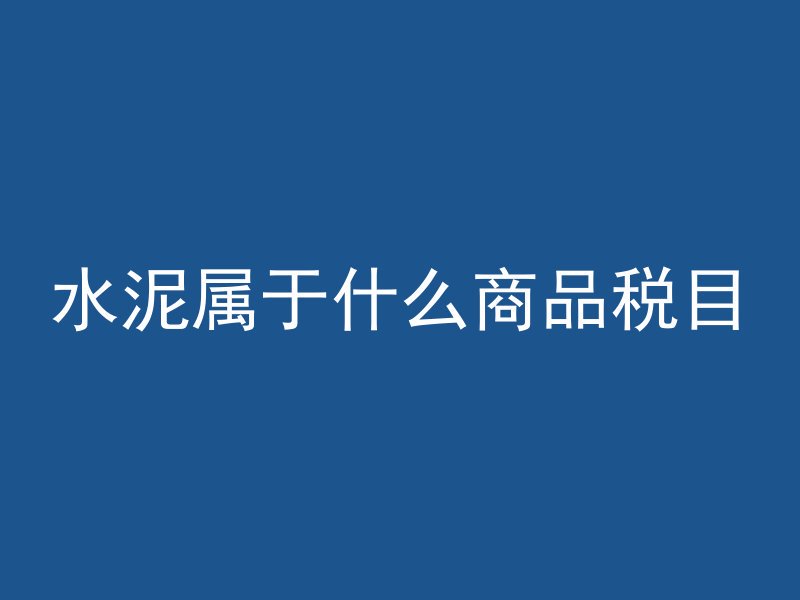
搅拌时间对混凝土内部气泡的生成有显著影响。搅拌不均匀会导致外加剂富集的区域产生过多气泡,而搅拌时间过长则会使混凝土中引入更多的气泡。
6. 脱模剂选择不当
某些脱模剂对气泡具有强吸附性,如机械厂回收的废机油,一旦气泡接触到这些脱模剂,就很难随着振捣而上升排出,导致混凝土结构表面出现气泡。
7. 振捣不充分或不均匀
振捣是使混凝土获得密实、排除气泡的重要手段。振捣时间不足、振捣强度不够、振捣密度过低或振捣过程不规范,都会导致气泡无法完全排出。分层振捣的高度和振捣器的插入间距也会影响气泡的排出。
8. 混凝土浇筑分层高度不合理
采用插入式振捣器时,混凝土的分层厚度应取决于振捣器的长度。分层厚度过大会超出振捣器的有效振捣深度,使气泡无法排出。
9. 模板表面粗糙
模板表面的光滑程度对气泡的产生也有影响。表面粗糙的模板更容易吸附气泡,使其难以排出。
10. 施工人员操作不当
施工人员擅自往混凝土里加水,以增加混凝土的工作性,但这样会增大混凝土的水灰比,进而影响混凝土的强度和耐久性,使气泡问题更加严重。
11. 掺合料使用不当
适量的掺合料如粉煤灰、矿渣粉等可以改善混凝土的和易性,减少气泡的产生。但掺加过量的掺合料会导致混凝土粘度增加,影响气泡的排出。
12. 温度变化的影响
混凝土受水泥水化热作用、大气及周围温度、电气焊接等因素影响而冷热变化时,会发生收缩和膨胀,从而产生表面气泡。
13. 坍落度控制不当
坍落度过小或过大都不利于气泡的排出。坍落度过小易形成粗骨料离析,不易振捣密实;坍落度过大则不易排气,且在振捣过程中易分层。
14. 配合比设计不合理
混凝土配合比设计不合理,如胶凝材料用量过多,会导致混凝土粘度增大,气泡不易排出。
15. 运输过程引入气泡
混凝土在运输过程中,由于运距过长或搅拌车对混凝土的搅拌,也可能引入过多的气泡。
混凝土梁板气泡多的原因涉及原材料、骨料级配、外加剂、水灰比、搅拌时间、脱模剂选择、振捣操作、浇筑分层高度、模板表面粗糙度、施工人员操作、掺合料使用、温度变化、坍落度控制、配合比设计以及运输过程等多个方面。要有效控制气泡问题,需要从这些方面入手,采取针对性的措施。