在混凝土浇筑过程中,楼板不振是一个常见的问题,它可能对楼板的强度和耐久性产生严重影响。本文将从多个方面探讨混凝土楼板不振的原因及解决方法。
1. 振动力不足
振动力不足是导致混凝土楼板不振的主要原因之一。如果混凝土振动器的频率和振幅不足以产生足够的振动力,就无法使混凝土中的空气充分排出,从而影响混凝土的密实度。为了解决这个问题,可以增加振动器的频率和振幅,或者更换为功率更大的振动器。
2. 混凝土粘稠度高
混凝土的粘稠度过高也是导致不振的原因之一。高粘稠度的混凝土在振动过程中会产生很大的阻力,使得振动器难以将混凝土中的空出。为了降低混凝土的粘稠度,可以适当调整混凝土的水灰比,增加用水量或采用减水剂等措施。
3. 振动时间不够
振动时间不足也会导致混凝土不振。如果振动时间不够,混凝土中的空气就无法被完全排出,从而影响混凝土的密实度。在浇筑混凝土时,应确保振动器有足够的振动时间,一般建议每点的振捣时间控制在20~30秒。
4. 振动器故障或保养不良
振动器本身出现故障或保养不良也可能导致不振。例如,振动器的轴承损坏、软轴扭断等问题都会影响其正常工作。定期对振动器进行维护和保养,确保其处于良好的工作状态,是预防不振问题的重要措施。
5. 混凝土原材料不均匀
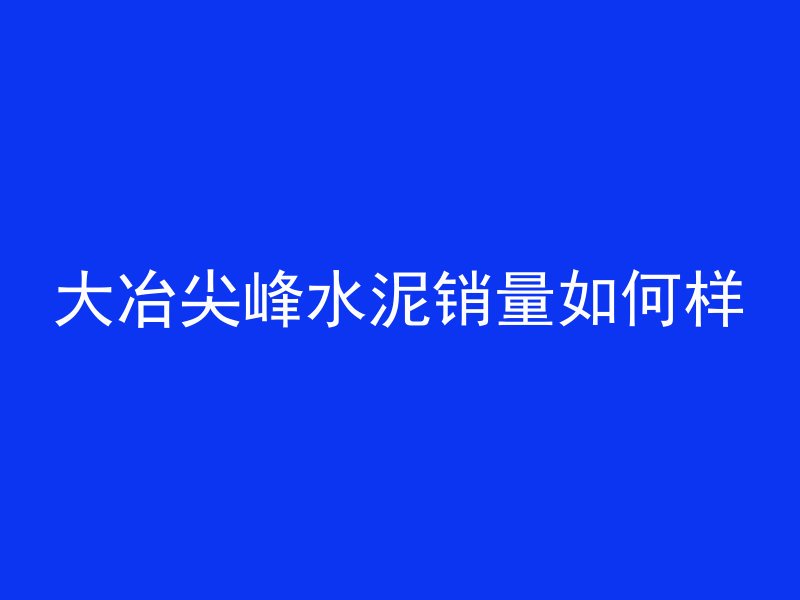
混凝土原材料的不均匀注入也是导致不振的原因之一。如果混凝土中的砂、石、水泥等材料分布不均匀,就可能导致振动过程中部分区域无法得到有效振动。在搅拌混凝土时,应确保原材料的均匀混合。
6. 施工操作不当
施工操作不当也可能导致混凝土楼板不振。例如,在浇筑混凝土时,如果振捣棒撞击钢筋或模板,就可能导致钢筋移位或模板破损,从而影响混凝土的振动效果。在施工过程中,应严格按照操作规程进行操作,避免对钢筋和模板造成损坏。
7. 钢筋密集处振动困难
在钢筋密集的区域,振动器的振动效果可能会受到影响。由于钢筋的阻挡,振动器可能无法将混凝土中的空气完全排出。为了解决这个问题,可以采用人工插捣或模皮锤敲击等辅助手段来增强振动效果。
8. 模板问题
模板的拼接不严密或表面粗糙也可能导致混凝土不振。如果模板的缝隙没有堵好或表面有杂物粘附,就可能导致混凝土在振动过程中漏浆或表面粗糙。在浇筑混凝土前,应确保模板的拼接严密且表面清洁。
9. 养护不当
养护不当也可能对混凝土的振动效果产生影响。如果混凝土在浇筑后没有得到充分的养护,就可能导致其表面出现裂缝或强度下降等问题。在浇筑混凝土后,应按照规范要求进行充分的养护。
10. 配合比不当
混凝土的配合比不当也可能导致不振。如果砂、石、水泥等材料的比例不合理或加水量过多过少,就可能导致混凝土的和易性差或离析现象严重。在搅拌混凝土时,应确保配合比的准确性并严格控制加水量。
11. 振捣顺序与时间不当
振捣的顺序与时间也是影响混凝土楼板不振的重要因素。如果振捣的顺序不合理或振捣时间不足,就可能导致部分区域无法得到有效振动。在振捣过程中应按照规范要求进行操作并严格控制振捣时间。
12. 振捣器操作方式不当
振捣器的操作方式也会影响其振动效果。如果操作不当如振捣棒插入过深或过浅、振动时间过长或过短等都可能导致不振问题。因此在使用振捣器时应掌握正确的操作方法如快插慢拔、上下抽动等以确保振动效果。
13. 泌水过多
对于截面积较大的墩柱或厚度较小、高度较大的薄壁桥台台身等结构在浇筑混凝土时可能会出现泌水过多的问题。泌水过多会导致混凝土表面出现浮浆层影响振动效果。为了防止这种情况的发生可以采取调整配合比、使用泌水性小的水泥等措施来减少泌水量。
14. 真空脱水与振动密实配合不当
在实际生产中常将真空脱水与振动密实配合使用以提高混凝土的密实度和强度。然而如果两者配合不当也可能导致不振问题。例如如果真空脱水时间过长或振动时间不足就可能导致混凝土表面出现鱼鳞纹或轻微离析现象。因此在使用真空脱水与振动密实配合时应掌握合适的操作程序和参数以确保混凝土的质量。
15. 楼板厚度浇筑不够
楼板厚度浇筑不够也可能导致不振问题。如果楼板厚度不足就无法提供足够的空间供振动器进行振动从而导致混凝土中的空气无法完全排出。因此在进行楼板浇筑时应确保楼板厚度达到设计要求以确保振动效果。
混凝土楼板不振问题可能由多种原因引起。为了解决这一问题,需要从多个方面入手,包括提高振动力、降低混凝土粘稠度、确保足够的振动时间、定期维护和保养振动器、确保原材料均匀混合、规范施工操作、采用辅助手段增强振动效果、确保模板拼接严密且表面清洁、充分养护混凝土、确保配合比准确、掌握正确的振捣顺序与时间以及操作方法等。只有综合考虑这些因素并采取有效的措施才能有效地解决混凝土楼板不振问题提高混凝土的强度和耐久性。