在建筑施工中,混凝土浇筑是一个至关重要的步骤,而抛光则是其后不可或缺的一环,它直接关乎到混凝土表面的美观度与耐久性。接下来,我们将深入探讨混凝土浇筑后如何进行有效抛光。
1. 抛光时机选择
抛光混凝土需选择合适时机,通常建议在混凝土初凝后、终凝前进行。此时混凝土表面已具备一定硬度,抛光效果**。过早抛光可能导致表面损伤,过晚则难以达到理想的光滑度。
2. 表面预处理
抛光前需对混凝土表面进行彻底清洁,去除浮浆、杂物及污渍。可使用高压水枪冲洗,必要时辅以专用清洁剂,确保表面干净无尘。还需检查并修补表面裂缝或缺陷,为抛光打下良好基础。
3. 选用合适抛光工具
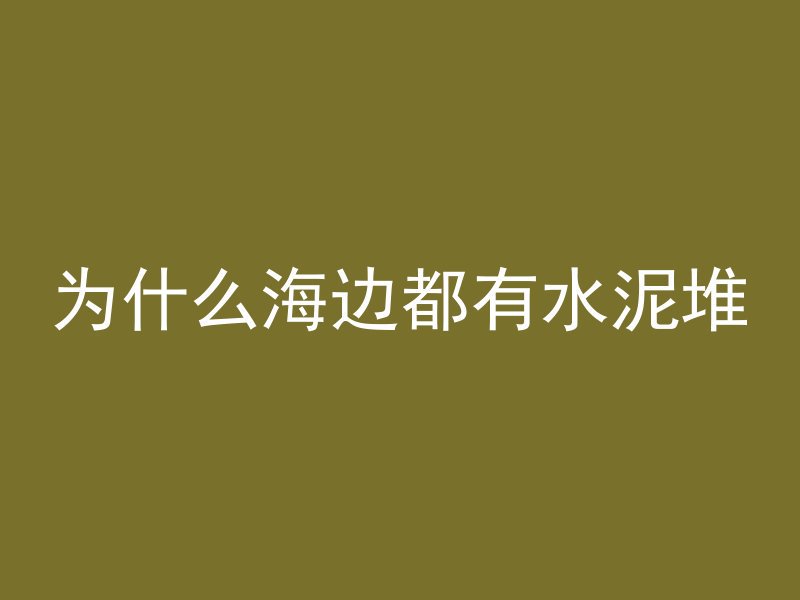
抛光工具的选择至关重要,需根据混凝土硬度、表面状况及抛光要求来确定。常用抛光工具包括金刚石磨片、树脂磨片及抛光垫等。初抛光阶段可选用较粗的磨片,逐渐过渡到细磨片及抛光垫,以达到更好的抛光效果。
4. 分阶段抛光
抛光过程应分阶段进行,先从粗磨开始,逐步过渡到中磨、细磨及最终抛光。每阶段需确保充分研磨,避免跳步操作,以保证抛光效果的均匀性。需根据抛光效果及时调整磨片或抛光垫的粒度。
5. 控制抛光速度
抛光速度对抛光效果有直接影响。速度过快可能导致表面烧伤或划痕,过慢则效率低下。需根据混凝土材质及抛光工具的特性,合理控制抛光速度,确保抛光质量。
6. 加水润滑
在抛光过程中,适时加水润滑可有效降低磨片与混凝土表面的摩擦,减少热量产生,避免表面损伤。水还能帮助清除研磨产生的粉尘,保持抛光环境的清洁。
7. 边缘处理
边缘部位由于空间限制,往往难以使用大型抛光设备。此时可采用手持式抛光机或手动工具进行细致处理,确保边缘与整体抛光效果一致。
8. 检查与修补
抛光完成后,需对混凝土表面进行全面检查,及时发现并修补抛光过程中产生的瑕疵或缺陷。对于局部不平整或光泽度不足的区域,可进行二次抛光或局部修补。
9. 养护与保护
抛光后的混凝土表面需进行养护,以提高其耐久性和抗污性。可采用专用养护剂进行喷涂或涂刷,形成保护膜。需避免在养护期间对表面造成划伤或污染。
混凝土浇筑后的抛光是一个复杂而细致的过程,需综合考虑多个因素并采取相应的措施。通过科学合理的抛光方法和技术手段,可以显著提升混凝土表面的美观度和耐久性,为建筑项目增添亮点。