混凝土放灰是混凝土建筑施工中的一个重要环节,它直接关系到混凝土的质量和工程的可靠性。本文将从多个方面详细阐述混凝土放灰的相关问题。
1. 放灰的定义与重要性
混凝土放灰是指在混凝土浇筑过程中,通过特定方式将灰浆(即混凝土中的水泥浆)均匀分布在混凝土中,以确保混凝土的强度和耐久性。这一步骤对于保证混凝土质量至关重要,因为灰浆的均匀分布能够增强混凝土的内部结构和整体性能。
2. 放灰时间的控制
在混凝土浇筑后的24小时内,不建议进行放灰操作。这是因为混凝土在这段时间内需要充分水化,以达到一定的强度。如果过早放灰,可能会破坏混凝土的内部结构,影响其质量。放灰时间的控制是确保混凝土质量的关键。
3. 放灰量的把握
放灰量直接影响混凝土的质量。放灰量过多会降低混凝土的强度,而过少则会影响浇筑质量。一般而言,放灰量应控制在混凝土总质量的1%至2%之间,即每立方米混凝土放灰量约为10升至20升。这一比例的把握需要施工人员的经验和专业技能。
4. 放灰位置的选择
放灰位置的选择也是操作中的关键环节。放灰口应对准搅拌机的中心轴线,以确保混凝土能够充分混合。放灰口周围应无阻碍物,避免无组分混凝土的出现。合理的放灰位置能够确保混凝土的均匀性和质量。
5. 罐车放灰前的清洗
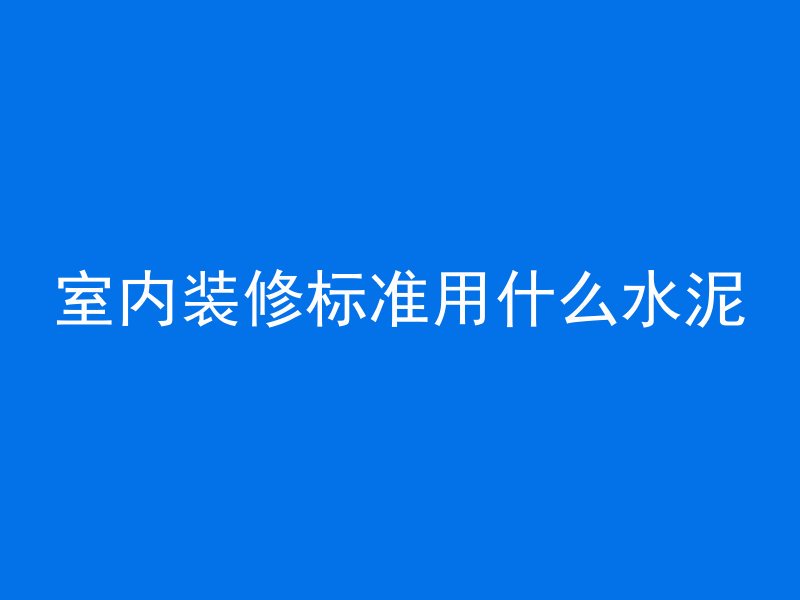
在放灰前,混凝土罐车应进行充分清洗,以清除残留混凝土。这一步骤能够防止新旧混凝土混合不均,影响混凝土质量。清洗罐车是确保混凝土纯净度和质量的重要措施。
6. 放灰后的及时养护
放灰后,混凝土需要及时进行养护,以防止水分过快蒸发导致表面开裂。养护方法包括覆盖保湿材料、喷洒养护剂等。充分的养护能够确保混凝土表面得到充分水化,提高其强度和耐久性。
7. 环境因素对放灰的影响
环境因素如温度、湿度和风速等也会对混凝土放灰产生影响。在高温、干燥或多风的环境下,混凝土表面的水分容易蒸发,导致泌水现象加剧。在这些环境下进行放灰操作时,需要更加注意控制放灰时间和量,以确保混凝土质量。
8. 施工质量对放灰的影响
施工质量不佳也是导致混凝土起灰起砂的原因之一。如果混凝土的配比、搅拌、浇筑等环节控制不当,会导致混凝土内部结构疏松,容易产生灰尘。在放灰前,需要确保施工质量符合规范要求,以减少起灰起砂的风险。
9. 水泥质量对放灰的影响
水泥质量也是影响混凝土放灰效果的重要因素。如果水泥是冒牌或过期潮湿的,将严重影响混凝土的强度和耐久性。在放灰前,需要确保水泥的质量符合标准要求。
10. 砂石料级配与含泥量
砂石料的级配不合理或含泥量高也会导致混凝土起灰起砂。骨料级配不合理或过细的土砂易导致地面起砂,影响水泥的早期水化及混凝土的凝结。在放灰前,需要对砂石料进行筛选和清洗,以确保其质量符合要求。
11. 施工过程中的过分振捣
过分振捣会加剧混凝土表面的泌水现象,导致混凝土表面强度降低。在放灰过程中,需要控制振捣力度和时间,避免过分振捣对混凝土质量产生不良影响。
12. 养护不当对放灰的影响
养护不当也是导致混凝土起灰起砂的原因之一。如果养护时间不足或养护方法不当,会导致混凝土表面水分大量蒸发,水泥水化不充分,从而降低混凝土强度。在放灰后,需要严格按照养护要求进行养护操作。
13. 使用防尘剂减少灰尘
为了减少混凝土表面的灰尘产生,可以在混凝土表面喷洒防尘剂。防尘剂能够渗透到混凝土内部,填充微小裂缝,提高混凝土的密实性和耐磨性。这一措施可以在一定程度上减少起灰起砂的风险。
14. 定期维护与清洁
对于已经出现的混凝土灰尘问题,可以采取定期清洁的方式进行处理。使用专业的清洁工具和清洁剂彻底清除混凝土表面的灰尘和污垢,保持其美观和使用效果。定期维护与清洁是延长混凝土使用寿命的重要措施之一。
15. 固化剂处理起砂起灰问题
对于已经出现的混凝土起砂起灰问题,可以使用混凝土硬化剂固化剂进行处理。这种处理方法能够增强混凝土表面的硬度和密实度,有效防止起砂起灰现象的发生。固化剂处理是一种经济实用的解决方案,广泛应用于厂房车间等地面处理中。
混凝土放灰是混凝土建筑施工中的一个重要环节,需要从多个方面进行严格控制和管理。通过合理控制放灰时间、把握放灰量、选择合适的放灰位置、充分清洗罐车、及时养护混凝土以及注意环境因素的影响等措施,可以确保混凝土放灰的质量和效果。针对已经出现的起砂起灰问题,可以采取定期清洁和固化剂处理等方法进行解决。