混凝土施工后,表面常出现浮灰现象,这不仅影响美观,还可能削弱混凝土的结构强度。这一现象的产生,涉及多个复杂因素,下面将从多个方面详细阐述混凝土打完表面浮灰多的原因。
1. 水灰比过大
水灰比过大是导致混凝土表面浮灰多的常见原因。在施工过程中,如果加入的水量超过了比例要求,会导致混凝土表层泌水,形成一层浮浆,从而降低混凝土表面的强度,产生浮灰。
2. 水泥标号过低或变质
水泥标号过低或水泥变质,如受潮结块,会影响水泥的水化反应,降低混凝土的强度。不合格的水泥无法与砂子形成有效的粘结,导致表面易起灰。
3. 砂子粒度过细或含泥量高
砂子的粒度过细会导致拌和时需水量增大,从而加大水灰比,降低强度。砂子含泥量高也会影响水泥与砂子的粘结力,使得混凝土表面容易出现浮灰。
4. 施工过程中的过分振捣
振捣是混凝土施工中的重要环节,但过分振捣会加剧混凝土表面的泌水情况,导致表面强度降低,后期容易出现浮灰。
5. 压光时间不当
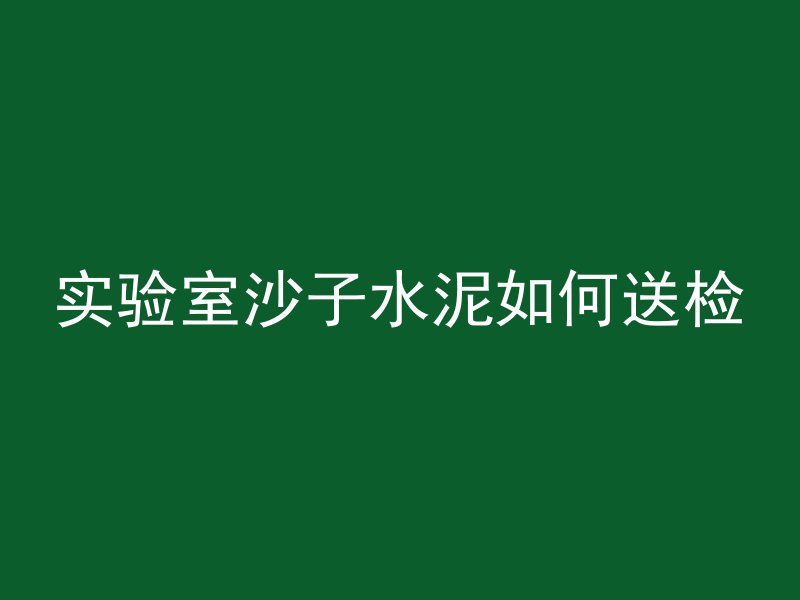
压光过早或过迟都会影响混凝土表面的质量。压光过早,水泥水化作用尚未完全,表面水分较多,易形成水光;压光过迟,则可能破坏已经硬结的表面,导致起砂起灰。
6. 养护不当
养护是混凝土施工后的重要环节。如果养护不及时或养护不充分,如太阳暴晒、大风天气导致混凝土表面大量失水,会降低混凝土强度,产生浮灰。
7. 泌水未处理
混凝土施工后,表面常有多余泌水。如果未及时刮去这些泌水,或在处理泌水时洒干拌水泥砂不均匀,都会导致表面强度降低,产生浮灰。
8. 骨料级配不合理
骨料级配不合理,如砂子粒度过细或过粗,都会影响混凝土的性能。过细的砂子需水量大,易导致水灰比增大;过粗的砂子则可能影响混凝土的粘聚力和强度。
9. 施工环境温度影响
环境温度对混凝土的水化反应有重要影响。在低温下施工,混凝土早期表面可能受冻,影响水泥的水化反应,导致表面强度降低,产生浮灰。
10. 添加剂使用不当
在混凝土中加入某些添加剂,如早强剂、减水剂等,如果使用不当,也可能影响混凝土的性能,导致表面浮灰。
11. 混凝土配合比不准确
混凝土配合比的不准确,如水泥、砂子、石子等原材料的用量不符合设计要求,也会影响混凝土的性能,导致表面浮灰。
12. 施工工艺不当
施工工艺的不当,如浇筑、振捣、抹平等环节的操作不规范,也可能影响混凝土表面的质量,导致浮灰的产生。
13. 原材料质量问题
原材料的质量问题,如水泥、砂子、石子等存在质量问题,也会影响混凝土的性能,导致表面浮灰。
14. 混凝土运输和浇筑过程中的问题
在混凝土运输和浇筑过程中,如果搅拌不均匀、离析等现象严重,也会影响混凝土的性能,导致表面浮灰。
15. 后期使用和维护不当
混凝土施工完成后,如果后期使用和维护不当,如过早上人、上物、上车作业等,也可能破坏混凝土表面的硬膜,导致浮灰的产生。
混凝土打完表面浮灰多的原因涉及多个方面,包括水灰比、水泥标号、砂子质量、施工过程、养护条件、环境温度、添加剂使用、配合比准确性、施工工艺、原材料质量、运输和浇筑过程以及后期使用和维护等。要有效解决这一问题,需要从多个方面入手,综合施策。