混凝土顶板起泡是建筑工程中常见的问题,它不仅影响美观,还可能削弱结构的整体性能。为了有效解决这个问题,需要从多个方面入手,确保施工质量和材料选择的合理性。
1. 调整配合比
配合比不合理是导致气泡产生的重要原因。粗集料过多而细集料不足,会导致混凝土内部空隙增大,气泡易于产生。需要合理调整粗细集料的比例,确保骨料级配合理,使混凝土更加密实。胶凝材料过多也会增加混凝土的粘度,使气泡难以排出。适当减少水泥等胶凝材料的使用量,可以降低混凝土的粘度,有利于气泡的排除。
2. 控制水胶比
水胶比过大是产生气泡的另一个关键因素。过多的水分会在混凝土内部形成气泡,且难以排出。需要严格控制水胶比,在满足混凝土强度要求的前提下,尽量减少用水量。选择强度等级稍低或物理技术性能指标偏差较小的水泥,增大水泥用量,也可以有效降低气泡的产生。
3. 选用优质模板和脱模剂
模板的材质和脱模剂的选择对气泡的产生也有重要影响。使用表面光滑、平整的模板可以减少气泡的产生。脱模剂要涂抹均匀但不宜过厚,避免气泡在模板上吸附。优选水性脱模剂,少用油性脱模剂,以减少气泡的吸附性。
4. 加强振捣
振捣是排除混凝土中气泡的重要手段。振捣时间、力度和频率都需要严格控制。振捣时间不足,气泡无法完全排出;振捣时间过长,则可能导致混凝土分层、泌水。需要选择适宜的振捣设备,确定**的振捣时间、半径和频率,确保气泡得到有效排除。
5. 控制外加剂掺量
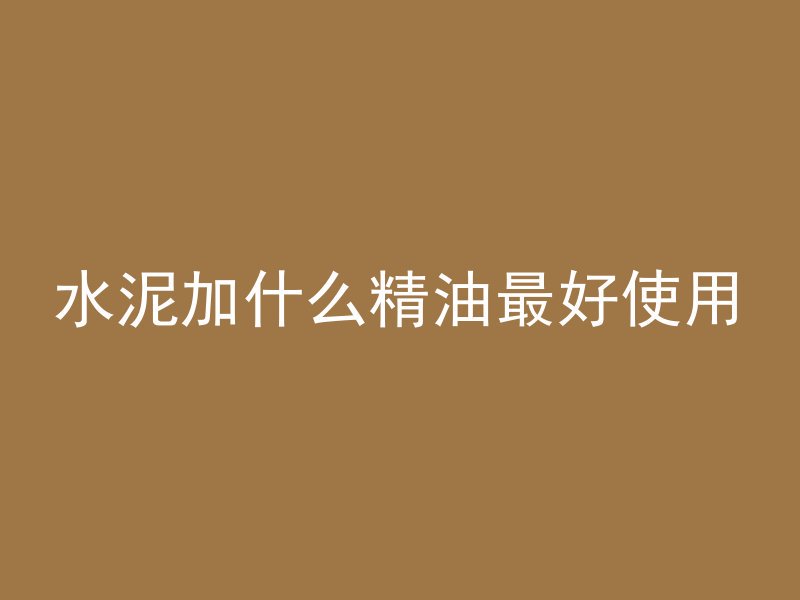
外加剂中引气成分的减水剂掺量过高也会导致气泡产生。需要严格控制外加剂的掺量,避免因过度引入气泡而导致气泡问题。对于高强度、高性能混凝土,应选用引气气泡小、分布稳定均匀的引气剂。
6. 均匀搅拌
混凝土的均匀搅拌对气泡的产生也有重要影响。不均匀的搅拌会导致外加剂在混凝土中分布不均,无法充分发挥其改善混凝土性能的作用。在生产过程中需要加强混凝土的均匀搅拌,确保外加剂在混凝土中的均匀分布。
7. 选用优质材料
材料的质量对混凝土的性能有着至关重要的影响。选用优良的矿物外加剂和水泥,严格控制骨料大小和针片状颗粒含量,可以有效减少气泡的产生。对于引气剂的选择也需谨慎,应选用能产生细小、分布均匀气泡的引气剂。
8. 建立排气通道
在模板上建立排气通道可以使混凝土表面光滑,提高施工质量。排气通道的设置可以根据混凝土的厚度和模板的材质等因素进行综合考虑,确保气泡能够有效排出。
9. 分层布料和振捣
在混凝土浇筑过程中,应采用分层布料和振捣的方法。每层的厚度不宜过大,一般不超过50cm,以确保气泡能够有效排出。振捣棒要插入下层混凝土中,确保上下层混凝土之间的密实度。
10. 及时处理和修补
对于已经产生的气泡,需要及时进行处理和修补。首先排查泡孔产生的原因,避免同样问题的重现。然后清理起泡处的松动部分,用混凝土修补剂进行修补,再用清水擦拭干净。
11. 控制现场砂石含水率
现场的砂石含水率变化也会影响混凝土的质量。如果未能及时准确调整因砂石含水率变化带来的配比调整,每车混凝土的坍落度将出现显著差异,进而影响气泡的生成与消除。需要定期检测砂石含水率,并根据检测结果及时调整配合比。
12. 选用合适的引气剂
引气剂的质量对混凝土表面产生的气泡有着本质的影响。对于高强度、高性能混凝土而言,必须选用那些能够产生细小、分布均匀气泡的引气剂,而尽量避免使用那些容易产生大气泡的引气剂。通过严格把控引气剂的质量,可以从源头上减少混凝土表面气泡的产生。
13. 注意温度变化
混凝土受水泥水化热作用、大气及周围温度、电气焊接等因素影响而冷热变化时,会发生收缩和膨胀,可能产生表面气泡。这些气泡的特征是随温度变化而扩张或合拢。在施工过程中需要注意温度控制,避免温度变化过大导致气泡产生。
14. 加强施工管理和培训
施工管理和培训也是减少气泡产生的重要环节。通过加强施工管理,确保施工过程的规范化和标准化;通过培训施工人员,提高他们的技能水平和质量意识,可以有效减少因施工不当导致的气泡问题。
15. 定期检查和维护设备
设备的性能状态对混凝土的质量也有重要影响。定期检查和维护设备,确保其正常运转和性能稳定,可以避免因设备故障导致的气泡问题。特别是对于振捣器等关键设备,更需要加强维护和保养。
解决混凝土顶板起泡问题需要从多个方面入手,包括调整配合比、控制水胶比、选用优质模板和脱模剂、加强振捣、控制外加剂掺量、均匀搅拌、选用优质材料、建立排气通道、分层布料和振捣、及时处理和修补、控制现场砂石含水率、选用合适的引气剂、注意温度变化、加强施工管理和培训以及定期检查和维护设备等。只有全方位、多角度地实施预防措施,才能有效控制气泡的产生,提高混凝土顶板的质量。