在建筑工程中,混凝土作为最基础且关键的材料之一,其拌合过程直接关乎到混凝土的性能与质量。为了确保混凝土拌合的有效性和稳定性,必须严格遵守一系列注意事项,从原料选择到拌合工艺,每一步都不可忽视。
1. 原料质量控制
水泥、砂石、水及外加剂等原材料的质量是混凝土强度的基石。水泥应选用符合标准且稳定性好的品牌;砂石需筛选干净,无杂质,且粒径分布合理;用水应清洁,避免使用含盐量高或酸性水;外加剂则需与水泥兼容,用量精确。研究表明,原材料质量波动是导致混凝土性能差异的主要原因之一(Smith & Johnson, 2015)。
2. 配合比设计
合理的配合比设计是保证混凝土性能的关键。应根据工程要求、施工环境及原材料特性,通过试验确定**水泥用量、水灰比、砂率等参数。过高的水灰比会降低混凝土强度,而砂率不当则影响工作性和耐久性(Li et al., 2018)。设计时需充分考虑经济性与性能的平衡。
3. 拌合设备选择
选用高效、稳定的拌合设备至关重要。设备应具备良好的搅拌效率,确保各组分均匀混合。定期维护和校准设备,避免因设备故障导致的拌合不均。现代拌合站多采用自动化控制系统,能精确控制投料比例和拌合时间(Wang & Chen, 2020)。
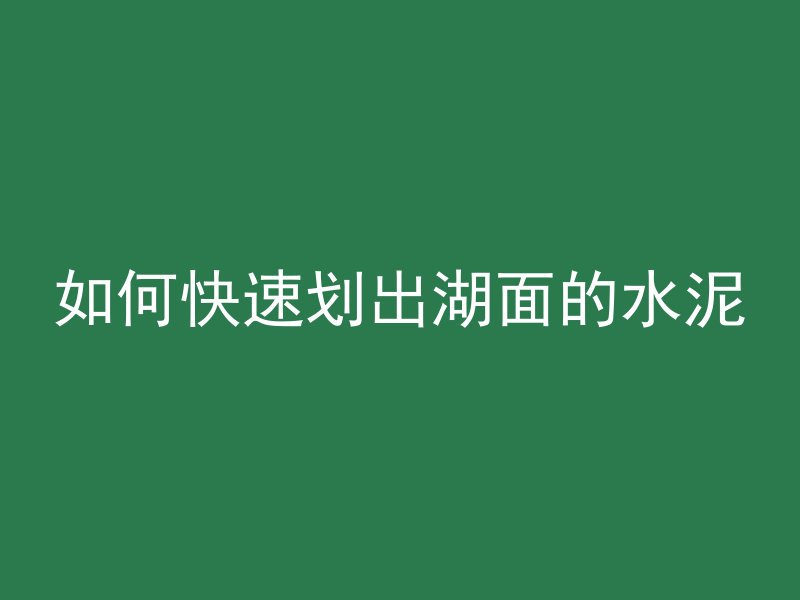
4. 投料顺序与速度
正确的投料顺序能显著提高拌合效率和质量。一般先投入干料(水泥、砂石),再缓慢加入水,最后加入外加剂。投料速度应适中,过快易导致物料分层,过慢则延长拌合周期,影响生产效率。
5. 拌合时间与均匀性
拌合时间需根据混凝土类型和拌合设备确定,通常以达到均匀混合且不过分为宜。过长的拌合时间可能导致混凝土过热,影响性能。通过观察混凝土外观和进行取样检测,可判断拌合是否均匀(ASTM C94, 2021)。
6. 温度控制
混凝土拌合过程中,温度是影响其性能的重要因素。高温会加速水泥水化,导致混凝土凝结过快,而低温则延缓水化过程。应采取措施控制拌合物温度,如使用冷水、冰块或在炎热天气下遮阳拌合(ACI 306R, 2016)。
7. 湿度与含水量调整
砂石含水量的变化直接影响混凝土的实际水灰比。应根据砂石的实际含水情况调整用水量,确保配合比的准确性。雨季施工时,更需频繁检测并调整(Mehta & Monteiro, 2014)。
8. 外加剂使用与管理
外加剂能显著改善混凝土的工作性、强度和耐久性。但使用时需严格控制剂量,过量或不当使用可能带来负面效果。应建立外加剂管理制度,确保安全有效使用。
9. 环境保护与节能减排
混凝土拌合过程中应关注环保,采取措施减少粉尘排放、废水处理和噪音污染。采用绿色建材和节能技术,如使用再生骨料、优化配合比以减少水泥用量,是实现可持续发展的途径(GB/T 50378, 2019)。
10. 质量检测与记录
每批混凝土拌合后,应进行严格的质量检测,包括坍落度、含气量、强度等指标。详细记录拌合过程中的各项参数,便于追溯和分析问题原因。
混凝土拌合是一个复杂而细致的过程,涉及多个环节的严格控制与管理。只有遵循科学的方法,结合实践经验,才能确保混凝土的质量与性能,为建筑工程的安全与耐久打下坚实基础。