防水混凝土是一种具有优良防水性能的建筑材料,广泛应用于地下室、隧道、水池等需要防水的工程结构中。防水混凝土的调配是一个复杂而精细的过程,涉及多个方面的控制和调整。以下将从多个方面详细阐述防水混凝土如何调配。
1. 原材料选择
防水混凝土与普通混凝土在原材料选择上有相似之处,但也有其特殊之处。水泥应选用普通硅酸盐水泥或火山灰质硅酸盐水泥,水泥强度等级不低于42.5级。砂宜选用中砂,含泥量≤3%。石子粒径应控制在一定范围内,一般不大于40mm,泵送时其最大粒径应小于输送管径的1/4。根据需要还可以掺入粉煤灰、硅粉等活性掺合料。
2. 配合比设计
防水混凝土的配合比设计至关重要。水泥用量不得少于320kg/m³,掺有活性掺合料时,水泥用量不得少于280kg/m³。砂率宜为35%~45%,泵送时可增至45%。灰砂比宜为1:1.5~1:2.5。水灰比一般不大于0.55,有侵蚀性介质时水胶比不宜大于0.45。防水混凝土的抗压强度和抗渗性能必须符合设计要求,抗渗水压值应比设计值提高0.2MPa。
3. 外加剂选择
根据工程需要,防水混凝土中可掺入各种外加剂,如引气剂、减水剂、三乙醇胺、氯化铁等。引气剂能增加混凝土中的微小气泡,提高抗冻性;减水剂能减少拌合用水量,提高混凝土强度;三乙醇胺能加速水泥水化,提高早期强度;氯化铁则能提高混凝土的密实性和抗渗性。
4. 搅拌与运输
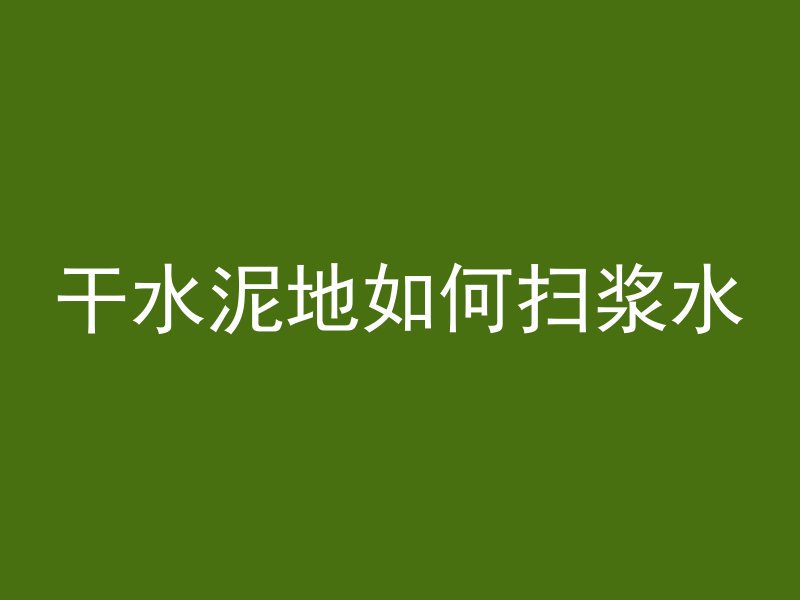
防水混凝土的搅拌应采用机械搅拌,搅拌时间比普通混凝土略长,一般不少于120s。掺入引气剂外加剂的混凝土,搅拌时间约为120~180s。在运输过程中,应防止漏浆、离析和坍落度损失。如出现离析,必须进行二次搅拌。当坍落度损失后不能满足施工要求时,应加入原水灰比的水泥浆或二次掺加减水剂进行搅拌,严禁直接加水。
5. 浇筑与振捣
防水混凝土的浇筑应严格做到分层连续进行,每层厚度不宜超过300~400mm,上下层浇筑的间隔时间一般不得超过2h。浇筑前,应清除模板内的积水、木屑等杂物,并用水湿润模板。防水混凝土应采用机械振捣,振捣时间宜为10~30s,以混凝土泛浆和不冒气泡为准,应避免漏振、欠振和超振。
6. 养护
防水混凝土的养护对其抗渗性能影响很大。在常温下,混凝土进入终凝(浇筑后4~6h)即应覆盖,并经常浇水养护,保持湿润不少于14天。防水混凝土不宜用电热养护和蒸汽养护,以免产生干缩裂缝或毛细管扩张,降低抗渗能力。
7. 施工缝处理
施工缝是防水结构容易发生渗漏的薄弱部位,应尽量减少施工缝的留置。如确需留设施工缝,应做好施工记录和处理工作。施工缝上下两层混凝土浇筑时间间隔不宜太长,以免接缝处新旧混凝土收缩值相差过大而产生裂缝。在继续浇筑混凝土前,应将水平施工缝处松散的混凝土凿除,清理浮渣和杂物,用水冲洗干净,保持湿润,再铺一层水泥砂浆。
8. 特殊部位处理
防水混凝土结构内的预埋件、穿墙管道、后浇带、变形缝等部位是防水处理的重点。预埋件宜预埋,埋设件端部或预留孔(槽)底部的混凝土厚度不得小于250mm。穿墙管道应采用套管加焊止水环的做法,确保振捣密实且不损坏管道。后浇带和变形缝应设置止水带或填塞密封材料,以满足密封防水、适应变形的要求。
9. 配合比试验与调整
防水混凝土的配合比应通过试验确定,并根据实际情况进行调整。在试验过程中,应关注混凝土的抗压强度、抗渗性能、坍落度等指标,确保满足设计要求。还应根据原材料的变化及时调整配合比,以保证混凝土的质量稳定。
10. 温度控制
在大体积防水混凝土施工中,温度控制是一个重要环节。应尽量选用低热或中热水泥,掺加适量粉煤灰或减水剂以降低水化热量。浇筑时应避开炎热天气,采用冰水或搅拌中掺加冰屑拌制混凝土。浇筑后应加强养护和测温工作,及时覆盖保温材料,使混凝土缓慢降温和收缩,减少裂缝的产生。
11. 质量控制与检验
防水混凝土的质量控制应贯穿于整个施工过程中。从原材料进场到混凝土浇筑、振捣、养护等各个环节都应严格控制质量。还应进行必要的检验和试验工作,如抗压强度试验、抗渗性能试验等,以确保混凝土的质量符合设计要求。
12. 安全环保措施
在防水混凝土施工过程中,还应采取必要的安全环保措施。如设置安全防护设施、加强施工人员的安全教育等,以确保施工安全。还应注重环境保护工作,如减少噪音污染、防止粉尘飞扬等。
防水混凝土的调配是一个复杂而精细的过程,涉及多个方面的控制和调整。只有严格按照设计要求进行施工和质量控制工作,才能确保防水混凝土的质量稳定并满足工程需求。